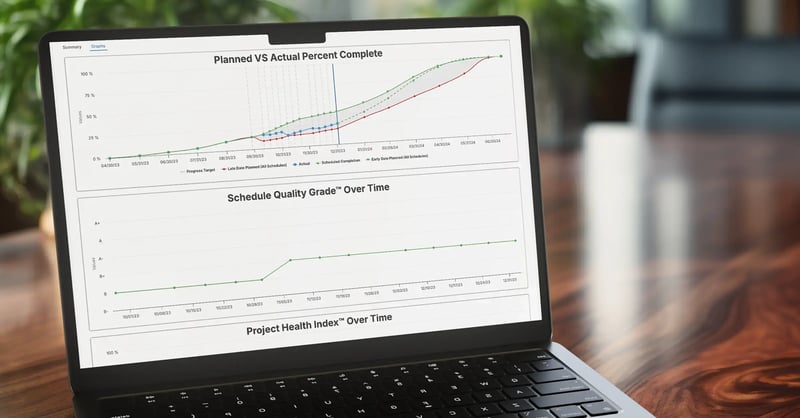
The construction industry is advancing rapidly, and staying competitive means embracing more innovative tools and strategies. One of the most impactful innovations today is predictive analytics in construction—a powerful approach reshaping how project data is interpreted, and decisions are made.
With SmartPM, construction professionals gain unprecedented control over their project schedules. By analyzing schedule data and extracting critical insights, SmartPM enables teams to identify risks early, enhance performance, and achieve better outcomes.
If you're looking to explore the power of predictive analytics in construction, you're in the right place. This blog explores strengthening your project controls and building a more data-driven, proactive construction process.
What are Predictive Analytics in Construction?
Predictive analytics in construction involves using data to anticipate outcomes and make informed decisions before issues arise. It means analyzing key project data, such as schedules, budgets, and performance metrics, to forecast challenges or opportunities ahead of time.
By applying advanced algorithms and leveraging historical trends, predictive analytics in construction uncovers risks, highlights inefficiencies, and recommends actions to keep projects on track.
Think of it as a data-powered crystal ball for your job sites. Rather than reacting to problems after they happen, project teams can act early—minimizing surprises, improving efficiency, and keeping budgets and timelines in check. Whether you're forecasting delays or spotting potential cost overruns, predictive analytics equips you to lead with confidence and control.
How Does Predictive Analytics Work?
Predictive analytics in construction relies on historical data, machine learning, and advanced algorithms to forecast outcomes and inform smarter decisions. The process begins with gathering large volumes of data, from past project performance and weather patterns to supply chain metrics, and analyzing them for meaningful trends and patterns.
Here’s how the process unfolds:
1. Data Collection
Accurate data is the foundation of predictive analytics. This involves collecting relevant information from diverse sources, including project schedules, resource logs, and external datasets. Ensuring this data is complete and representative is critical for meaningful insights.
2. Data Processing
Raw data must be cleaned and formatted prior to being utilized. This includes handling missing values, removing duplicates, and normalizing data. Proper processing ensures your predictive models are both reliable and actionable.
3. Feature Selection and Engineering
Not all data points are useful. Feature selection identifies which variables most influence outcomes, while feature engineering enhances data by creating or transforming variables to better represent underlying patterns—both essential steps in refining model accuracy.
4. Model Building
With the data prepared, a statistical or machine learning model is trained to identify patterns or forecast future scenarios. You might use regression, classification, or clustering models to address specific construction challenges depending on your objectives.
5. Model Evaluation
Before implementation, models are evaluated for performance using metrics like accuracy, precision, or F1 score. This validation step ensures your analytics tools deliver dependable results.
6. Deployment and Monitoring
Once proven effective, the model is deployed in real-time environments and integrated with construction platforms like SmartPM. Continuous monitoring helps maintain accuracy and adapt to evolving project conditions.
5 Types of Predictive Analytics Techniques
Predictive analytics in construction draws on several core techniques to uncover insights and forecast future outcomes. Each method provides a unique lens for interpreting project data, helping teams make proactive, data-driven decisions.
Here are five foundational techniques that power predictive analytics in construction:
1. Regression Analysis
Regression helps quantify relationships between variables, such as how changes in crew size might impact project duration. It’s widely used for forecasting trends, identifying key drivers, and informing scheduling or budget decisions.
2. Classification
Classification models group data into predefined categories. In construction, this might mean flagging projects as high, medium, or low risk based on historical performance indicators. These models help teams prioritize attention where it’s needed most.
3. Time Series Analysis
This method analyzes data over time to detect trends, seasonality, or cyclical patterns. For construction professionals, it’s essential for tracking progress, forecasting schedules, and identifying anomalies before they disrupt the timeline.
4. Clustering
Clustering groups similar data points without predefined labels. It’s useful for segmenting projects, identifying common risk factors, or revealing hidden performance patterns across job sites.
5. Neural Networks
Inspired by the human brain, neural networks are capable of modeling complex relationships in large datasets. They’re increasingly used in construction for advanced applications like image recognition on job sites, predictive safety analysis, and smart automation.
Each of these techniques contributes to the broader impact of predictive analytics in construction, enabling teams to see beyond the present and plan with precision.
10 Ways to Leverage Predictive Analytics in Construction
Construction professionals are increasingly using data analytics to enhance operations and improve outcomes across projects. By adopting advanced analytical tools, teams gain actionable insights into timelines, costs, and resource deployment.
Among these tools, predictive analytics stands out. It helps teams anticipate potential issues, refine workflows, and drive smarter decision-making. This forward-looking approach is reshaping the construction landscape—supporting more efficient, resilient, and sustainable project delivery.
Below are ten practical ways predictive analytics is transforming construction:
Forecast New Growth Opportunities
Use predictive models to identify where your business can grow. By analyzing historical trends and current market data, construction leaders can spot emerging opportunities—whether it’s expanding services, investing in new regions, or adjusting to shifts in client demand.
This proactive strategy not only enhances competitiveness but also positions your business to capitalize on market trends early, driving long-term growth and innovation.
Support Risk Management
Predictive tools help you pinpoint and manage risks before they derail your project. By monitoring real-time data and project indicators, you can anticipate issues like cost overruns, schedule delays, and compliance gaps.
Early intervention allows for targeted mitigation strategies, which protect project performance and strengthen client confidence.
Enhance Sales Processes
Modernize your sales processes by using data-driven insights to target the right clients at the right time. Predictive models help identify potential customer needs, enabling your sales team to personalize pitches and close deals more effectively.
In the construction industry, predictive analytics can play a vital role in the bidding process by providing accurate insight into project timelines, labor availability, and potential scheduling conflicts. By analyzing historical project data and external factors, companies can create more accurate schedules during the bidding phase, strengthening their proposals with realistic timelines and resource planning.
This strategic approach not only boosts your chances of winning bids but also ensures that project execution aligns closely with planned schedules. Additionally, forecasting demand for services allows you to allocate resources more efficiently, build relationships that support long-term growth, and ultimately enhance both sales outcomes and operational performance.
Project Planning and Scheduling
Predictive analytics in construction enhances project planning by delivering data-backed insights that streamline timelines and resource use. By identifying potential bottlenecks and forecasting delays, teams can better sequence tasks and avoid workflow disruptions.
This approach improves coordination across teams, reduces schedule overruns, and supports more predictable project delivery—helping ensure jobs stay on track and within scope.
Worksite Optimization
Optimize job site efficiency through predictive models that analyze labor distribution, equipment utilization, and materials management. With predictive analytics in construction, you can pinpoint operational inefficiencies and make real-time adjustments.
By aligning resources and workflows more effectively, construction managers improve productivity, reduce downtime, and create safer, more responsive worksites.
Cost Estimation and Budgeting
Transform your approach to cost control with predictive tools that generate accurate, data-informed estimates. By evaluating historical project data and specific job requirements, you can forecast costs more precisely and proactively manage budgets.
This strengthens financial planning, prevents cost overruns, and builds client confidence with transparent, reliable numbers from the start.
Resource Allocation
Predictive analytics in construction helps teams match the right resources to the right tasks, minimizing waste and maximizing impact. Analyze project scope, labor capacity, and equipment needs to ensure optimal resource allocation across all phases.
Efficient resource use supports timely delivery, controls costs, and enhances overall project performance.
Equipment Maintenance
Use predictive models to anticipate maintenance needs before equipment failure disrupts your schedule. By monitoring usage data and wear patterns, construction teams can plan preventive maintenance that reduces downtime and extends equipment life.
Well-maintained machinery keeps projects running smoothly, improves job site safety, and avoids last-minute repair costs.
Quality Control
Integrate predictive analytics into your quality control processes to detect issues early and ensure compliance. Analyzing past project data reveals patterns that highlight areas of risk or recurring defects.
Proactive quality assurance not only enhances outcomes but also supports better client satisfaction and long-term credibility.
Supply Chain Management
Predictive analytics in construction brings visibility to your supply chain. By assessing demand trends and supplier reliability, you can improve procurement strategies and prevent material delays.
Smart planning ensures you get the right materials at the right time, minimizing waste, avoiding work stoppages, and keeping your project momentum strong.
What Does the Future Hold for Predictive Analytics in Construction?
The future of predictive analytics in construction is bright and rapidly evolving. As the industry continues to digitize, advanced analytics tools are poised to tackle some of its most persistent challenges, including cost overruns, schedule delays, and resource inefficiencies.
One of the most promising developments is the integration of predictive analytics with smart technologies like digital twins. These virtual replicas of construction projects simulate real-world conditions, enabling teams to visualize potential outcomes before a single task begins. With predictive models driving these simulations, stakeholders can proactively resolve design flaws, mitigate cost risks, and streamline execution.
Additionally, the rise of IoT devices on job sites is generating real-time data that enhances model accuracy. This live feedback loop strengthens the predictive power of analytics, allowing for immediate adjustments and continuous performance improvements.
Another key trend is smarter labor and equipment management. Predictive analytics enables more precise forecasting of staffing needs and maintenance schedules, helping reduce downtime, enhance safety, and keep projects moving efficiently. Algorithms can also identify patterns in safety incidents, supporting more effective prevention strategies.
Ultimately, predictive analytics in construction is not just about technology—it’s about building a culture of foresight and continuous improvement. Companies that embrace this mindset will be positioned to deliver higher-quality work, adapt to changing demands, and lead the industry into a more innovative, data-driven future.
Conclusion
Predictive analytics in construction is reshaping how the industry plans, executes and delivers projects. By turning raw data into actionable insights, construction teams can proactively manage risk, improve efficiency, and drive stronger outcomes at every stage.
As the industry continues to evolve, construction firms that embrace predictive analytics will be better equipped to stay competitive, control costs, and deliver consistent value. This isn't just a trend. It’s a strategic advantage.
SmartPM is at the forefront of this transformation. As a leading construction management solution, it empowers teams with predictive analytics to streamline schedules, anticipate challenges, and make smarter decisions with confidence.
Ready to take your construction projects to the next level? Learn how SmartPM can help you harness the power of predictive analytics—schedule a demo today.
Share