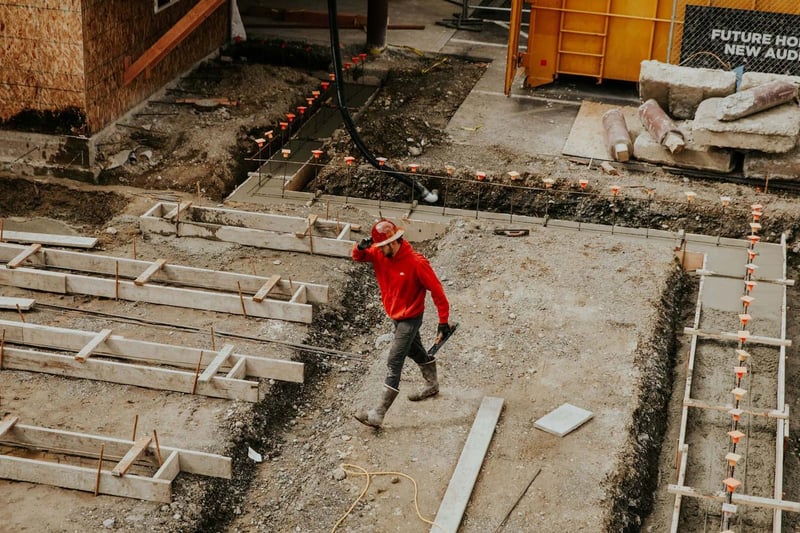
Blog
20 Construction Company Risks and Mitigation Strategies
From safety hazards to budget overruns, uncover the key risks in construction and learn practical approaches to safeguard your business.
Managing construction projects comes with a variety of challenges, from unforeseen delays to budget overruns and compliance risks. Left unchecked, these risks can jeopardize a project's success and impact profitability.
However, proactive strategies and advanced tools can protect your projects from potential pitfalls. This guide explores 20 common risks faced by construction companies and effective mitigation strategies to keep your projects on track.
Leverage the power of SmartPM to analyze your schedule data and gain actionable insights for better project outcomes. Start mitigating risks today—empower your construction projects with SmartPM!
What is Risk in Construction?
Risk in construction refers to the possibility of events or conditions that can adversely affect the outcome of a project. These risks can stem from numerous sources, including financial challenges, unforeseen site conditions, labor shortages, supply chain delays, weather-related interruptions, or changes in project scope.
Each of these factors has the potential to disrupt timelines, inflate costs, and diminish overall project quality if not addressed proactively.
For construction project managers and firms, mitigating risks is crucial to ensure projects are completed on time, within budget, and to the required standards. Effective construction risk management improves decision-making, minimizes costly disruptions, and enhances operational efficiency.
Additionally, it demonstrates reliability to stakeholders, fosters trust, and ultimately safeguards profitability. Without a well-structured approach to identifying, assessing, and managing risks, construction firms are more vulnerable to unexpected challenges that could derail their success.
Identifying Risks During Construction Projects
For construction project managers, identifying potential risks is a critical part of ensuring successful project outcomes. Construction projects are inherently complex, involving numerous stakeholders, tight timelines, intricate designs, and various environmental and regulatory factors.
By pinpointing risks early in the process, project managers can address issues before they escalate, avoiding construction delays, cost overruns, or safety incidents.
Risk identification also supports more accurate project planning and resource allocation. It enables managers to create contingency plans, maintain realistic schedules, and allocate budgets effectively.
Furthermore, addressing risks upfront reinforces trust and transparency with clients and stakeholders, demonstrating a commitment to diligent project oversight. Without a thorough understanding of potential risks, projects face a higher likelihood of unexpected interruptions that can compromise their overall success and reputation.
Encountering Risks in During Different Construction Phases
Construction projects are dynamic endeavors where risks can vary significantly across different phases. By acknowledging and addressing these risks as they arise, project teams can mitigate their impact and maintain progress toward successful completion. Below, we'll explore how risks manifest during each construction phase and strategies to address them.
Pre-Construction Phase
The pre-construction phase is critical for laying the groundwork of a project, but it is also where several risks can emerge and potentially derail progress before construction begins. One of the primary risks during this phase arises from inadequate planning and unclear project scopes.
Poorly defined objectives, incomplete designs, or missing specifications can lead to miscommunications and costly revisions later. Additionally, budgeting and scheduling risks are prevalent, as inaccurate cost estimations or unrealistic timelines can limit the feasibility and sustainability of the project.
Another significant risk comes from regulatory and permitting requirements. Failing to account for zoning laws, environmental regulations, or approval delays may result in setbacks or even legal implications. Stakeholder disagreements and inconsistent communication during pre-construction also pose risks, as decisions made at this stage affect the entire project's trajectory.
To mitigate these risks, it is essential to employ detailed planning, thorough risk assessments, and clear communication strategies. Regular coordination with stakeholders, obtaining accurate cost data, and ensuring compliance with legal and regulatory requirements are vital to safeguarding the project’s integrity and preparing for the execution stage.
Construction-and-Settlement Phase
The construction-and-settlement phase carries its own unique set of risks that, if not properly managed, can jeopardize the project timeline, budget, and overall success. One significant risk is schedule delays, which can arise from unforeseen circumstances such as poor weather conditions, labor shortages, or supply chain disruptions. These delays not only slow progress but also lead to cost overruns that compound financial pressures.
Another critical risk is the potential for quality issues or deviations from design specifications. Poor workmanship, inadequate supervision, or the use of substandard materials can compromise the structural integrity and functionality of the project, leading to expensive rework or safety hazards.
Additionally, this phase often involves on-site health and safety risks, where insufficient safety measures or lapses in compliance can result in accidents, harming workers and increasing liability costs.
Effective communication breakdowns between contractors, subcontractors, and stakeholders can further hinder progress during this phase. Misaligned expectations or poorly documented changes can lead to conflicts, legal disputes, or misunderstandings about project deliverables.
To mitigate these risks, implementing robust project management practices, maintaining rigorous quality control processes, and adhering to safety regulations are imperative. Regular progress monitoring and adaptive problem-solving are also essential to ensuring the project reaches completion efficiently and successfully.
The Construction Company Risk Management Process
Effective construction risk management involves a systematic approach to identifying, assessing, and mitigating potential challenges throughout the project lifecycle. By proactively addressing risks, project managers can safeguard timelines, budgets, and quality standards, ensuring successful outcomes.
The following key areas provide a framework for comprehensive risk management in construction projects:
Avoid Project Risk
Risk avoidance involves taking proactive measures to eliminate potential threats before they can impact the project. This approach requires identifying high-risk scenarios early and making adjustments to ensure they are avoided altogether.
For example, revising project plans to exclude risky elements, adjusting timelines to give teams more flexibility, or modifying processes to eliminate vulnerabilities are common strategies. This method ensures that the project is steered toward safer, more manageable paths, ultimately reducing the likelihood of encountering major setbacks.
Transfer the Project Risk
Risk transfer involves shifting the responsibility for managing a specific risk to a third party, such as an insurance company, subcontractors, or outsourcing vendors. This strategy is often used when a risk requires specialized expertise or resources that the project team does not possess.
For example, purchasing an insurance policy to cover unforeseen events or outsourcing a complex task to a skilled vendor reduces the burden on the project team while ensuring the risk is handled by those equipped to manage it. While transferring risk typically comes with a cost, it provides peace of mind and allows the team to focus on other aspects of the project.
Mitigate the Project Risk
Risk mitigation reduces the impact of risks through targeted actions that directly address potential issues. This approach often involves increasing safety measures, improving quality control processes, or allocating additional resources to areas with higher risk exposure.
For instance, implementing stricter compliance standards, conducting regular audits, or providing additional training to team members working on critical tasks can significantly lower the chances of problems occurring. By addressing risks proactively, mitigation strategies help ensure the project delivers desired outcomes and stays on track.
Accept Project Risk
In some cases, risks cannot be avoided, transferred, or mitigated due to their low probability of occurrence, minimal potential impact, or impracticality of managing them. When this happens, the project team may choose to accept the risk and address any consequences if and when they arise. This approach requires careful assessment and monitoring to ensure that the accepted risks do not spiral out of control.
For example, a small budget overrun might be an acceptable risk if the cost of avoiding or mitigating it outweighs the impact. By acknowledging these risks and preparing for possible outcomes, teams can maintain focus without overextending resources.
20 Construction Company Risks and How to Mitigate Them
Construction projects are complex and fraught with potential risks that can impact timelines, budgets, and overall project outcomes. Identifying these risks early and having a clear strategy for managing them is critical to ensuring success.
The following sections outline 20 key risks commonly encountered in the construction industry, along with practical mitigation strategies to address them effectively. By proactively addressing these risks, project teams can improve efficiency, reduce costly delays, and ensure high-quality results.
Delays
Delays are one of the most common and costly risks in the construction industry, often leading to budget overruns, stakeholder dissatisfaction, and disrupted schedules.
Various factors can contribute to delays, including weather conditions, labor shortages, unforeseen site conditions, and delays in material deliveries. These issues can create a domino effect if not seen and addressed proactively, slowing progress and piling on additional expenses as timelines stretch and resources remain tied up.
Here are practical strategies project managers can employ:
- Detailed Planning - Develop a comprehensive project schedule with realistic timelines, accounting for potential hold-ups and critical milestones. Utilize tools like Gantt charts or project management software to track progress.
- Risk Assessment - Conduct thorough risk assessments during the planning phase to identify potential delay factors and prepare contingency plans.
- Real-Time Delay Analysis – Monitor delays as they happen to understand their root causes and project-wide impact. Use historical and current schedule data to test the feasibility of mitigation strategies before implementation, ensuring that corrective actions are both timely and effective.
- Clear Communication - Foster open lines of communication between all stakeholders, including contractors, suppliers, and clients, to ensure that updates and issues are addressed promptly.
- Adequate Resource Allocation - Secure skilled labor and ensure that materials are ordered and delivered on time, reducing the possibility of bottlenecks.
- Weather Contingency Plans - Build buffer time into schedules to accommodate unexpected delays caused by adverse weather conditions.
By employing these mitigation strategies, project managers can significantly reduce the impact of delays, keep projects on track, and maintain stakeholder confidence.
Documentation Errors
Documentation errors pose significant risks in the construction industry as they can lead to miscommunication, legal disputes, budget overruns, and delays.
When contracts, blueprints, permits, or project plans contain inaccuracies, the entire project workflow may suffer, resulting in confusion among teams and costly mistakes during execution. The complexity of construction projects makes precise and accurate documentation critical to ensuring all stakeholders are aligned and informed throughout the process.
Implement the following strategies to mitigate the risks associated with documentation errors:
- Establish Rigorous Review Processes - Incorporate multiple layers of review and approval for all key documents to catch errors before they impact the project.
- Leverage Digital Tools - Use construction management software or document control platforms to maintain version control, track changes, and ensure consistency across documents.
- Provide Proper Training - Ensure all team members involved in documentation are trained on industry standards, software tools, and the importance of accuracy in record-keeping.
- Maintain Clear Communication Channels - Foster open communication between all stakeholders to quickly address any ambiguities or discrepancies in documentation.
- Schedule Regular Audits - Conduct periodic audits of the project documentation to identify and correct errors or omissions before they escalate into larger issues.
By prioritizing detailed and error-free documentation, project managers can enhance operational efficiency, reduce risks, and maintain the integrity of construction projects.
Miscommunication
Miscommunication in the construction industry can pose significant risks, leading to cost overruns, project delays, safety hazards, and compromised quality. With multiple stakeholders involved—including architects, contractors, suppliers, and clients—ensuring clear and accurate communication at every stage of the project is essential.
Communication breakdown often results in errors, rework, and conflicts, all of which can undermine the success of a construction project. Additionally, language barriers, poorly written instructions, and misinterpretations can exacerbate these challenges, making effective communication a critical priority.
To reduce the risks associated with miscommunication, construction companies can adopt the following strategies:
- Standardize Communication Protocols - Establish clear communication protocols, including standardized formats for documentation, reporting, and instructions. This minimizes ambiguity and ensures all stakeholders are on the same page.
- Utilize Technology - Leverage construction management software and digital communication tools to streamline information sharing, track updates in real-time, and provide centralized access to important data.
- Offer Training Programs - Provide communication and language training to ensure the workforce has the necessary skills to understand and convey critical information effectively.
- Encourage Collaborative Meetings - Host regular collaborative meetings where stakeholders can share insights, clarify expectations, and address potential misunderstandings before they impact the project.
- Inspect and Clarify Instructions - Double-check plans, diagrams, and other instructions for clarity and correctness, and provide opportunities for workers to ask questions if the instructions are unclear.
- Assign Communication Liaisons - Designate specific team members to act as liaisons between different groups, ensuring consistent messaging and reducing the risk of information being lost or misinterpreted.
By actively addressing communication challenges, construction companies can enhance project efficiency, prevent costly mistakes, and ensure the timely and successful delivery of construction projects.
Poor Risk Assessment
Poor risk assessment in construction projects can result in unforeseen problems that delay progress, inflate costs, and compromise safety. When risks are not adequately evaluated or managed, issues such as misallocation of resources, design flaws, and safety hazards can arise.
This lack of preparation leaves projects vulnerable to disruptions, legal conflicts, and reputational damage. Without proactive identification and mitigation of risks, even small oversights can escalate into significant challenges, jeopardizing the overall success of the project.
To minimize risks, construction companies can implement the following strategies:
- Develop Comprehensive Risk Management Plans - Create detailed plans outlining potential risks and their mitigation strategies, ensuring all team members are aligned.
- Conduct Regular Risk Assessments - Periodically review and update risk assessments as the project progresses to account for evolving circumstances.
- Engage Experienced Risk Analysts - Consult with industry experts and risk specialists to enhance the accuracy of risk evaluations.
- Encourage Team Collaboration - Foster communication among all stakeholders to ensure potential risks are identified early and addressed collectively.
- Invest in Training Programs - Equip workers and managers with the knowledge to recognize and handle risks effectively through ongoing training.
- Utilize Technology and Data Analytics - Leverage project management software and data analysis tools to monitor risk factors and predict potential issues before they materialize.
By prioritizing risk assessment and adopting these strategies, construction companies can reduce the likelihood of setbacks, maintain project continuity, and deliver successful outcomes.
Unsuccessful Change Management
Unsuccessful change management can significantly increase risks in the construction industry, as projects often involve complex processes, tight schedules, and multiple stakeholders. Poorly managed changes can lead to miscommunication, budget overruns, delays, and even compromised safety standards.
For instance, unexpected modifications to project designs or schedules without proper planning and coordination can disrupt workflows, cause resource shortages, and reduce overall efficiency.
To mitigate risks associated with unsuccessful change management, construction companies can adopt the following strategies:
- Establish a Clear Change Management Process - Develop a structured process for evaluating, approving, and implementing changes to ensure transparency and consistency across all project stages.
- Communicate Effectively - Maintain open communication channels to keep all stakeholders informed about potential changes and their implications, minimizing confusion and resistance.
- Conduct Impact Assessments - Analyze the potential effects of proposed changes on project timelines, budgets, and resource allocation before implementation to avoid unforeseen challenges.
- Train Project Teams - Provide team members with training on change management practices to ensure they are equipped to handle adjustments efficiently and effectively.
- Monitor Changes Continuously - Use project management tools to track and document changes in real time, ensuring proper oversight and minimizing the risk of errors.
By implementing these strategies, construction companies can handle changes more effectively, reducing disruptions and maintaining project success.
Subcontractor Default
Subcontractor default poses a significant risk in the construction industry, as the failure of a subcontractor to fulfill their obligations can lead to project delays, increased costs, and even legal disputes. This risk is further compounded by the complexity and scale of many construction projects, where multiple subcontractors are responsible for critical components of the work.
Subcontractor default can occur for various reasons, including financial instability, inability to meet project requirements or mismanagement. When a subcontractor defaults, contractors are often left scrambling to find replacements, which can disrupt timelines and budgets, ultimately impacting the project’s overall success and client satisfaction.
To minimize the impact of subcontractor default, construction companies can implement several proactive strategies:
- Thorough Vetting Process - Conduct comprehensive background checks and prequalification assessments to ensure subcontractors have the financial stability, technical expertise, and capacity to complete their assigned tasks effectively.
- Strong Contractual Agreements - Use detailed contracts that clearly define expectations, performance standards, and consequences of non-compliance. This provides a legal framework to mitigate risks and safeguard the project.
- Performance Bonds and Insurance - Require subcontractors to provide performance bonds or carry appropriate insurance coverage. These measures protect the contractor financially in the event of default.
- Regular Performance Monitoring - Continuously assess subcontractor performance throughout the project, using milestones and key performance indicators (KPIs) to identify and address issues before they escalate.
- Building Strong Relationships - Foster collaborative and transparent relationships with subcontractors to promote mutual trust and accountability. Open communication can often prevent misunderstandings that lead to default.
By incorporating these practices, construction companies can reduce the likelihood of subcontractor default and mitigate its impact, ensuring smoother project execution and protecting both timelines and budgets.
Supply Chain Issues
Supply chain issues present significant risks in the construction industry due to their potential to delay projects, increase costs, and disrupt workflows. Construction projects rely on the timely delivery of materials, equipment, and other resources.
Any disruption, such as shortages, shipping delays, or unexpected price surges, can lead to cascading effects throughout the project lifecycle. These issues are often compounded by global economic pressures, geopolitical events, and natural disasters, which can further destabilize the availability and affordability of critical supplies.
To mitigate the risks posed by supply chain issues, construction companies can adopt several proactive strategies:
- Diversify Suppliers - Relying on one supplier can be risky. Establish relationships with multiple vendors and explore local sourcing options to reduce dependency on distant or unstable markets.
- Implement Robust Inventory Management - Maintain accurate inventory tracking and ensure adequate stockpiling of essential materials to buffer against supply disruptions.
- Strengthen Supplier Relationships - Build strong partnerships with suppliers through consistent communication and fair dealings. Collaborative relationships can lead to priority treatment during supply shortages.
- Forecast Material Needs Early - Engage in detailed project planning to anticipate material requirements well in advance. Early procurement reduces the risk of last-minute shortages and cost escalations.
- Leverage Technology - Utilize digital tools and procurement software to monitor supply chain trends, assess risks, and enhance decision-making processes.
By adopting these practices, construction companies can create more resilient supply chains, minimize disruptions, and maintain project timelines and budgets, even in the face of unforeseen challenges.
Poor Project Management
Poor project management poses significant risks to construction projects by leading to delays, budget overruns, and compromised quality. Without effective planning and coordination, teams may face miscommunications, unclear responsibilities, and inefficient resource allocation.
Furthermore, inadequate oversight can result in missed deadlines, increased costs, and even safety hazards on-site. These issues not only affect the project's profitability but can also damage a construction company's reputation and client relationships.
- Develop Clear Objectives and Plans - Establish well-defined project goals and detailed plans to guide all phases of construction. Clear documentation ensures all stakeholders understand their roles and responsibilities.
- Invest in Skilled Project Managers - Employ experienced project managers who possess strong leadership, communication, and organizational skills to oversee the project's execution effectively.
- Prioritize Communication - Foster open and consistent communication among all team members to address issues quickly and maintain alignment across departments.
- Utilize Project Management Software - Implement tools that help track progress, monitor budgets, schedule tasks, and manage resources efficiently.
- Conduct Regular Training - Provide ongoing training for staff to keep them up-to-date with the latest construction standards, technologies, and management practices.
- Monitor Progress and Adapt - Conduct frequent progress reviews to identify potential problems early and adjust plans as necessary to keep the project on track.
By addressing the challenges of poor project management with these strategies, construction companies can create more efficient workflows, minimize risks, and ensure the successful delivery of projects.
Labor Shortages
Labor shortages pose significant risks to the construction industry, impacting project timelines, budgets, and overall quality. A lack of skilled workers can lead to delays in project completion, increased labor costs due to competition for qualified employees, and reduced efficiency on-site.
Additionally, overburdened teams may experience burnout, further exacerbating the issue and affecting worker safety.
To mitigate labor shortages, construction companies can adopt several strategies:
- Invest in Workforce Development - Offer training programs, apprenticeships, and certifications to upskill existing employees and attract new talent to the industry.
- Enhance Recruitment Efforts - Develop targeted recruitment campaigns to reach underrepresented groups, including women, veterans, and younger workers, to diversify and expand the labor pool.
- Collaborate with Educational Institutions - Partner with trade schools, colleges, and universities to promote careers in construction and create a pipeline of skilled workers.
- Improve Work Conditions - Provide competitive wages, benefits, and a safe, inclusive work environment to retain employees and reduce turnover.
- Leverage Technology - Implement advanced tools like automation and robotics to offset labor shortages by improving efficiency and reducing reliance on manual labor.
By proactively addressing labor shortages with these initiatives, construction companies can create a more sustainable workforce, maintain productivity, and secure their long-term success in the industry.
Poorly Defined Scope of Work
A poorly defined scope of work can pose significant risks in the construction industry, leading to confusion, project delays, budget overruns, and strained client relationships. When the scope of a project is ambiguous or incomplete, stakeholders may have differing expectations, resulting in disputes and rework.
Furthermore, without clear definitions, it becomes challenging to allocate resources efficiently, track progress, or identify accountability for specific tasks, ultimately jeopardizing the project’s success.
- Conduct Thorough Initial Planning - Engage all stakeholders during the planning phase to ensure a detailed and mutually agreed-upon scope of work.
- Develop Comprehensive Documentation - Create clear and detailed project documentation, specifying deliverables, timelines, budgets, and responsibilities.
- Utilize Technology for Clarity - Leverage project management software and Building Information Modeling (BIM) tools to visualize and define project parameters effectively.
- Implement Change Management Procedures - Establish a structured process for handling changes to the scope to avoid scope creep and miscommunication.
- Regularly Review and Communicate - Schedule frequent meetings to review progress and ensure all parties remain aligned with the scope throughout the project lifecycle.
By taking these steps, construction companies can minimize the risks associated with a poorly defined scope of work, ensuring smoother project execution and greater client satisfaction.
Health and Safety Hazards
Health and safety hazards pose significant risks in the construction industry due to the nature of the work environment. Construction sites often involve heavy machinery, working at heights, hazardous materials, and dynamic conditions, all of which increase the potential for accidents or injuries.
Without proper precautions, these hazards can lead to serious consequences, such as physical harm to workers, delays in project timelines, and financial liabilities for construction companies. Furthermore, failing to prioritize safety can damage a company's reputation and lead to legal or regulatory penalties.
To reduce health and safety risks, construction companies must implement comprehensive safety protocols and foster a culture of awareness. Key measures include:
- Conducting Regular Risk Assessments - Identify potential hazards on-site and evaluate their likelihood and impact. This proactive approach allows for timely mitigation strategies.
- Providing Comprehensive Training - Equip workers with the knowledge and skills they need to operate machinery, handle materials, and follow safety protocols effectively.
- Ensuring Use of Personal Protective Equipment (PPE) - Mandate and supply PPE such as helmets, gloves, safety goggles, and harnesses to minimize injury risks.
- Enforcing Strict Compliance with Regulations - Adhere to local, state, and federal safety guidelines to ensure that construction practices meet the highest safety standards.
- Promoting a Reporting Culture - Encourage workers to report unsafe practices or near-misses without fear of reprisal, enabling continuous improvement.
By addressing health and safety hazards proactively, construction companies can protect their workforce, minimize project disruptions, and maintain compliance with industry regulations, ultimately fostering a safer and more efficient work environment.
Payment Disputes
Payment disputes are a significant risk in the construction industry due to the complex nature of projects, involving multiple stakeholders, extensive timelines, and substantial financial investments.
These disputes can arise from delayed payments, unclear contract terms, scope changes, or disagreements over completed work quality. When left unresolved, payment disputes can disrupt cash flow, stall project progress, damage professional relationships, and even lead to costly legal battles or insolvencies.
- Establish Clear Contracts - Draft detailed contracts that outline payment schedules, deliverables, and procedures for addressing changes or disputes. This transparency helps manage expectations from the start.
- Maintain Accurate Documentation - Keep thorough records of agreements, invoices, change orders, and project updates. Proper documentation can provide evidence and clarity if disputes arise.
- Verify Payment Terms Early - Ensure all parties involved understand and agree to payment terms before the project begins. This includes milestones, due dates, and consequences for late payments.
- Use Construction Software - Leverage technology to track progress, manage invoices, and monitor payment timelines, reducing the likelihood of miscommunication or errors.
- Encourage Open Communication - Promote consistent and clear communication between all stakeholders to address potential issues early and collaboratively resolve disputes before they escalate.
By proactively addressing payment dispute risks, construction companies can protect their financial stability, enhance trust among stakeholders, and ensure smoother project execution.
Managing Change Orders
Change orders are a common occurrence in construction projects, but they inherently carry a variety of risks that can impact project timelines, budgets, and relationships. Unmanaged or poorly handled change orders can result in delays, cost overruns, and disputes between stakeholders.
Miscommunication about the scope or cost of changes can erode trust and lead to dissatisfaction among clients or subcontractors. Additionally, an inefficient process for managing change orders can stall decision-making and hinder progress.
Construction companies can implement the following practices to mitigate risks associated with change orders:
- Establish a Clear Change Order Process - Define and communicate a standardized process for submitting, reviewing, and approving change orders. Ensuring all parties understand this process reduces the chances of confusion or delays.
- Document Everything - Thoroughly document all change order requests, including detailed descriptions, cost estimates, and potential impacts on timelines. Proper documentation protects all parties and provides a clear record of agreed-upon adjustments.
- Assess Impacts Before Approval - Evaluate the potential effects of a change order on the project scope, budget, and schedule before approving. This prevents unfavorable decisions that could lead to disputes later.
- Foster Transparent Communication - Maintain open and honest communication between clients, contractors, and subcontractors to ensure all parties understand the necessity and implications of a change order.
- Monitor Budget and Contingencies - Regularly track project costs and maintain a contingency fund to cover unexpected expenses arising from change orders. This financial planning minimizes the risk of cost overruns.
By proactively managing change orders, construction companies can reduce risks, maintain project stability, and promote better collaboration between stakeholders, ensuring successful project outcomes.
Site Conditions
Site conditions play a crucial role in the execution of construction projects and can pose significant risks if not properly assessed and managed. Unexpected site conditions, such as unstable soil, hidden underground utilities, or environmental hazards, can lead to delays, increased costs, or even safety issues. These risks often stem from incomplete or inaccurate site assessments conducted during the planning phase.
To mitigate the risks associated with site conditions, construction companies should adopt the following practices:
- Conduct Comprehensive Site Assessments - Perform detailed surveys and tests to identify potential challenges before construction begins, such as soil stability, water drainage, or contamination.
- Review Historical Data - Examine records and past usage of the site to uncover any hidden issues, such as buried infrastructure or environmental concerns.
- Engage Experts Early - Collaborate with geotechnical engineers, environmental consultants, and other specialists to evaluate site conditions accurately.
- Include Site Risk in Project Planning - Account for potential site-related risks during the budgeting and scheduling phases to ensure adequate resources and time are allocated to address unforeseen issues.
- Implement Contingency Measures - Establish contingency plans and reserve funds to manage unexpected challenges that arise from site conditions efficiently.
By taking these proactive steps, construction companies can better manage site conditions, ultimately reducing project risks, improving safety, and maintaining project timelines and budgets.
Poorly Written Contracts
Poorly written contracts present significant risks in the construction industry, often leading to misunderstandings, disputes, delays, and financial losses. Ambiguities or omissions in contract terms can create confusion among stakeholders, resulting in misaligned expectations or unintentional non-compliance.
Ineffective contracts may also fail to adequately address critical areas such as payment schedules, change orders, dispute resolution mechanisms, or scope of work, exacerbating project risks and increasing the likelihood of costly litigation.
To mitigate the risks posed by poorly written contracts, construction companies can implement the following measures:
- Engage Legal Experts - Consult experienced construction attorneys to draft, review, or revise contracts, ensuring terms are precise, comprehensive, and legally enforceable.
- Standardize Contract Templates - Develop and use standardized contract templates that cover all essential aspects while reducing variability and potential errors during negotiations.
- Include Specificity and Clarity - Ensure all contract clauses are clear, detailed, and unambiguous to prevent misinterpretation or disputes between parties.
- Clearly Define Risk Allocation - Accurately outline responsibilities and liabilities for each party, identifying who bears specific risks to minimize confusion during the project lifecycle.
- Address Contingency Provisions - Incorporate contingency clauses for potential changes such as schedule delays, scope adjustments, or unforeseen expenses.
- Facilitate Regular Reviews - Conduct periodic contract reviews in collaboration with legal counsel and project stakeholders to identify and address gaps or emerging risks.
By prioritizing the development of robust, detailed contracts, construction companies can reduce the likelihood of disputes, safeguard project timelines, and enhance overall project outcomes.
Material Cost Fluctuations
Material cost fluctuations pose a significant risk to construction projects due to their potential to disrupt budgets and affect overall profitability.
Prices for essential materials like steel, lumber, and concrete can vary widely due to factors such as global demand, supply chain disruptions, tariffs, or economic instability. Unanticipated increases in material costs can lead to project delays, strained contractor-client relationships, and financial losses.
To address this challenge, construction companies can implement several proactive measures:
- Include Price Escalation Clauses - Incorporate provisions in contracts that account for potential material price changes, ensuring both parties agree on how such fluctuations will be managed.
- Bulk Purchasing Agreements - Secure long-term agreements with suppliers to lock in prices and ensure consistent material availability throughout the project lifecycle.
- Diversify Supply Chains - Work with multiple suppliers to reduce reliance on a single source and mitigate risks associated with supply chain disruptions.
- Monitor Market Trends - Stay informed about market conditions and emerging trends to anticipate price changes and adapt procurement strategies accordingly.
- Establish Contingency Budgets - Allocate a portion of the project budget to cover unexpected increases in material costs, reducing the potential impact on overall finances.
By implementing these strategies, construction companies can better manage the risks associated with material cost fluctuations, ensuring projects stay on track and within budget.
Availability of Materials
The availability of materials poses a significant risk to construction projects, as delays or shortages can disrupt timelines, increase costs, and impact project quality.
Fluctuations in supply chains can be influenced by factors such as global demand, natural disasters, political instability, or transportation issues. These challenges can leave construction companies struggling to secure essential materials in a timely and cost-effective manner.
To mitigate the risks associated with material availability, construction companies can adopt the following strategies:
- Develop Strong Supplier Relationships - Build reliable partnerships with multiple suppliers to ensure access to materials, even during times of high demand or supply chain challenges.
- Diversify Material Sources - Avoid sole reliance on a single supplier or geographic location by sourcing materials from several vendors and regions.
- Invest in Inventory Management - Maintain an adequate stock of critical materials to prevent project delays caused by unexpected shortages.
- Monitor Supply Chain Risks - Stay informed of potential disruptions in the global supply chain, such as political or economic changes, and adjust procurement plans accordingly.
- Plan for Substitute Materials - Identify and approve alternative materials that can replace unavailable options without compromising quality or safety.
- Leverage Technology for Forecasting - Utilize advanced tools and software to predict demand and plan procurement schedules more effectively.
By proactively addressing material availability risks, construction companies can reduce uncertainty, improve efficiency, and maintain progress on their projects despite external challenges.
Equipment Theft and Damage
Equipment theft and damage pose significant risks in the construction industry, often leading to costly delays, project disruptions, and financial losses. Construction sites, with their valuable machinery and tools, are frequent targets for theft. Additionally, equipment is susceptible to accidental or weather-related damage, further complicating project timelines.
- Secure the Job Site - Install fences, surveillance cameras, and proper lighting to deter unauthorized access and monitor activity around the clock.
- Inventory and Tracking Systems - Use equipment tracking technologies, such as GPS or RFID tags, to monitor the location and usage of tools and machinery.
- Implement Access Controls - Restrict equipment usage to authorized personnel only through keycard systems, PIN codes, or biometric verification.
- Regular Maintenance and Inspections - Conduct routine maintenance to ensure machinery is in optimal working condition, minimizing the risk of accidental damage.
- Insurance Coverage - Invest in comprehensive insurance policies to protect against financial losses arising from theft or damage.
- On-Site Security Personnel - Employ trained security guards to patrol the job site during and after working hours, enhancing safety and reducing potential risks.
- Develop an Emergency Response Plan - Establish protocols for responding promptly to incidents of theft or damage to minimize delays and ensure efficient recovery.
By implementing these preventive measures, construction companies can safeguard their equipment, maintain project continuity, and reduce the financial impact of theft or damage.
Weather Conditions and Natural Disasters
Weather conditions and natural disasters pose significant risks in the construction industry, often leading to delays, increased costs, and potential safety hazards. Unpredictable events such as heavy rain, strong winds, extreme heat, snowstorms, or more severe occurrences like hurricanes, earthquakes, or floods can disrupt project timelines and damage equipment or structures.
To mitigate these risks, construction companies can implement the following strategies:
- Monitor Weather Forecasts - Use reliable weather monitoring systems to anticipate changes in conditions and adjust schedules or activities accordingly.
- Implement Protective Measures - Secure materials and equipment by using tarps, physical barriers, or on-site storage that is resistant to weather elements.
- Develop a Contingency Plan - Prepare for delays by building flexibility into project timelines and maintaining an emergency response plan for severe weather or disasters.
- Train Workers on Safety Protocols - Ensure that all crew members understand safety procedures for working in adverse weather conditions, such as extreme heat or cold.
- Invest in Durable and Weather-Resistant Materials - Use construction materials designed to withstand local environmental challenges to minimize long-term damage or degradation.
- Establish Clear Communication - Maintain open lines of communication between management, workers, and stakeholders to quickly address and adapt to weather-related issues.
- Maintain Adequate Insurance Coverage - Protect against financial losses by securing insurance policies that cover weather-related damage and natural disasters.
By proactively addressing the risks posed by weather conditions and natural disasters, construction companies can enhance the safety of their sites, protect their investments, and ensure project continuity even in challenging circumstances.
Conclusion
Effectively managing risks in the construction industry is critical to ensuring safety, project success, and financial stability. The 20 risks and mitigation strategies discussed above highlight the wide-ranging challenges faced by construction companies, from weather-related disruptions to regulatory compliance and workforce management.
By implementing proactive measures and leveraging best practices, companies can minimize vulnerabilities and build resilience in their operations.
For a more comprehensive approach to risk management and project analytics, consider partnering with SmartPM. Our data-driven solutions provide valuable insights that help businesses optimize performance, improve decision-making, and deliver projects on time and within budget.
Visit SmartPM today to learn how we can support your construction projects.
Share