Schedule forecasting helps you watch for surprises on your construction projects. Utilizing a CPM schedule offers project teams abundant data that, if leveraged correctly, is critical for effectively managing contractual deadlines. All of the data within construction schedules have the potential to give insight into what is driving project deliverables. ‘
Having an accurate gauge for deliverables may seem impossible. Yet, it is achievable through data-driven schedule forecasting. This article examines schedule forecasting so project teams can efficiently manage toward an end date.
How to Ensure an Accurate Construction Schedule Forecast
Before explaining forecasting, it is important to note other project controls that must be available to you before you try predicting end dates. Over the past couple of months, SmartPM has expanded its knowledge base surrounding the importance of project controls within commercial construction. Before you even begin utilizing other schedule controls, you must have a high-quality CPM schedule.
Schedule forecasts are predictions of project conditions in the future based on information available at the time of schedule creation. How does forecasting accurately predict future project conditions? By utilizing historical performance data to determine the average production rate, you can use that information for the whole project. It can also be used for individual trades. Additionally, you can use this rate to predict a project’s future outcome if productivity remains the same. It should be noted that the more granular your data, the more reliable your forecasting will be.
As your project progresses, the forecast should also be updated, taking into account any changes in productivity. As the forecast is updated, it becomes a critical component in risk mitigation. Adjusting the schedule based on historical performance gives the best gauge for when a project will finish and what is driving its completion.
Schedule forecasting can be done in many different ways. However, forecasting can be done automatically by utilizing Earned Value Analysis (EVA) metrics and extrapolating that data on a future planned curve based on historical performance. To do this analysis, you will need the project’s Schedule Performance Index (SPI), which is calculated by dividing the project’s earned value by its planned value.
Utilizing Earned Value Analysis KPIs for Construction Schedule Forecasts
Don’t worry. There is no need to conduct a holistic earned value analysis to forecast. You only need to figure out two metrics, the planned value (PV) and earned value (EV):
- Planned Value (PV): the planned progress scheduled for completion at a specific point in time, represented as a percentage of the completion of the project (100%).
- Earned Value (EV)- the progress actually achieved at a specific point in time, represented as a percentage of the overall completion of a project (100%).
By looking at earned value over time, you can extract a Schedule Performance Index (SPI). The SPI acts as an indicator of project performance to date. It also can predict the outcome of the project if performance stays the same.
What is Schedule Performance Index (SPI)?
Using an earned value approach, SPI compares planned progress with earned progress to determine how closely you follow your baseline. A project’s SPI can be found by dividing its earned value by its planned value (EV/PV).
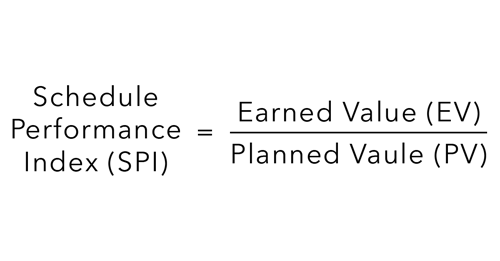
From there, the SPI’s ratio tells you where you are regarding progress. For this example, let’s say you conducted this analysis when you were 72% done with your project. However, you had originally planned to be 99% done at the current point in time.
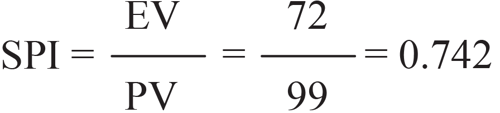
Recall that:
- SPI > 1 : Ahead of Schedule
- SPI < 1 : Behind Schedule
- SPI = 1 : On Schedule
Therefore, an SPI of 0.742 means that the project is achieving 74.2% productivity and is behind schedule. In other words, for every ten days of work, the project only earns 7.42 days of its planned work. So, if an activity has an original duration of 10 days, it will take 13.4 days to complete. This is because the production rate is slower than originally planned.
At What Point in the Project Lifecycle are Construction Schedule Forecasts Accurate?
The SPI becomes a trustworthy measure of performance halfway through the project. By this stage, there is sufficient data to ensure that any anomalies have minimal impact on the SPI. Essentially, at different phases of a project, there are different activities with different parties responsible for the work being done. So, it would not be fair to use delays during the pre-construction phase to adjust the construction phase as the problems you encounter would be different.
Halfway through the job, or, in this case, 72% through the job, project teams can forecast how they will perform in the future. They do this by looking at the entire schedule and using historical information to predict the future. By looking at the SPI of approximately 0.742, you can expect the estimated duration remaining will be about 34% longer. This is because, historically, the project is consistently underperforming by about 34%.
Planned vs. Actual Percent Complete
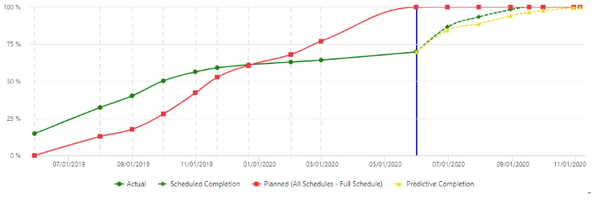
As depicted in the graph above, the project’s progress curve is extrapolated by using the SPI. The SPI adjusts the scheduled completion, shown by the yellow line. The yellow line is the schedule forecast. It predicts the project will be 100% completed about four months later than what the scheduled completion date is telling you and six months later than the baseline plan indicated.
Knowing this, decisions can be made to increase productivity (or manpower to accelerate), or the project will be delayed. If acceleration measures are met, the SPI will decrease, making the forecasted end date improve as a result of cured performance improvement.
What are the Benefits of Construction Schedule Forecasting?
Forecasting gives companies an early warning sign for potential end-date slippage. Knowing how much overrun you are potentially going to have opens lines of communication with all stakeholders, allowing for better outcomes for everyone through collaborative decision-making. Additionally, combining forecasting with other data-driven project control metrics throughout the entire duration of a project gives an unbiased gauge of when a project will actually finish.
As we conclude our series on project controls, it is important to note how automated project controls change how the construction industry is run by leveling the playing field between companies of any size. Through analyzing CPM schedules, actual project performance factors driving the end date become visible, project delivery becomes optimized, and relationships improve, as does an organization’s profitability.