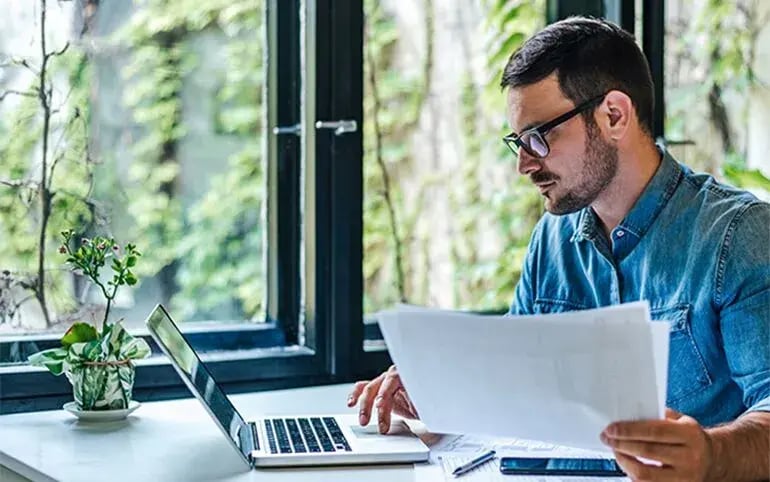
Blog
Construction Risk Management with Schedule Data
Analyzing schedule data has revolutionized how construction risks are identified and managed. By scrutinizing the schedule, you can pinpoint micro (project) and macro (organizational) risks.

Analyzing schedule data has revolutionized how construction risks are identified and managed. By scrutinizing the schedule, you can pinpoint micro (project) and macro (organizational) risks.
Construction risk management is a complicated subject. Given the many risks inherent in the construction industry, it’s easy to see why. One study reported that 77% of all construction projects suffer significant delays, with inadequate risk management being one of the primary reasons. What’s more, drawing on insights from KPMG’s 2023 Global Construction Survey it’s evident that the sector is grappling with challenges in meeting budget and schedule targets.
Check our complete guide on Construction Risk Management for strategies to identify, assess, and control risks for safer, more successful building projects.
A pivotal element in addressing these challenges is the strategic analysis of schedule data. By having access to schedule analytics across projects, firms can uncover patterns and risks that may not be apparent when projects are viewed in isolation, offering a path toward more effective risk management and improved project outcomes. This methodology not only aids in steering clear of common pitfalls but also gives the necessary visibility to allocate resources more efficiently, ensuring that projects are completed on time and within budget.
Identifying Organizational Risks with Schedule Data
Analyzing schedule data has revolutionized how construction risks are identified and managed. By scrutinizing the schedule, you can pinpoint micro (project) and macro (organizational) risks. This dual analysis aids in spotting trends or recurring issues across a range of projects, providing a clearer picture of your company’s overall risk profile.
This approach includes examining key factors such as planned versus actual progress, schedule quality, and the effectiveness of current risk management strategies. By doing so, you can proactively address potential issues, enhancing the health and viability of your projects.
Project-Level Analytics Begin with Quality Schedules
At the project level, various risk categories emerge. For example, you can view planned and actual progress discrepancies, schedule quality integrity, and predictive analytics. These assessments are crucial as they reveal the direct relationship between project health and the level of risk.
A robust project, exemplified by a high-quality schedule and accurate progress tracking, typically faces fewer risks. Unfortunately, not all schedules are created equal. Some are well-constructed, flexible, and informative, while others are not so much. The difference can be attributed to two primary factors:
- The person developing the schedule. Too many industry professionals are creating project schedules who don’t truly have the necessary skill set or experience.
- Bad data: Autodesk and management consulting firm FMI Corporation released the results of a study in 2021 that estimated the following.
- “Bad data – data that is inaccurate, incomplete, inaccessible, or untimely, and can’t be used to derive actionable insights – may have cost the global construction industry $1.85 trillion.”
Even the most well-developed schedule won’t provide much insight unless the analysis tool you use is as robust as the project. The complexity and dynamics of modern projects require advanced analysis tools that can handle the intricacies of the schedule, allowing for detailed tracking, forecasting, and scenario analysis. SmartPM, with its comprehensive features, serves as such a tool, effectively translating detailed schedules into actionable insights that guide risk management and decision-making. With these insights in hand, the next crucial step is to use them in formulating a comprehensive risk management plan.
How can a company determine the quality of its current schedule data and identify areas for improvement?
Determining the quality of current schedule data involves a thorough review of the schedule’s completeness, accuracy, logic, and adherence to industry best practices. This can be achieved by conducting an audit of the schedule to identify any gaps, inconsistencies, or unrealistic timelines.
The audit should assess whether the schedule encompasses all necessary activities, follows a logical sequence without errors or discrepancies, and aligns with the project’s scope and objectives. Improvements might involve refining activity durations, ensuring logic is correctly tied, and updating the schedule to reflect actual progress and changes in project scope – with assured buy-in from respective parties.
Developing a Construction Risk Management Plan
Once you’ve assessed your risks, it’s time to develop a risk management plan. Bear in mind that risk management is a continuous process, as setting up a single plan without regular review and revision leaves you vulnerable to future risks. Here are the steps:
1. Identify Risks
As you might expect, risk identification is the first step. Thoroughly review your contracts, policies, market conditions, and, most importantly, your project schedule data. With the help of technology, this data quickly shows patterns of delays, inconsistencies, and other risk factors across multiple projects. Doing so involves an analysis of schedule quality, which can reveal high float, missing logic, or trade stacking that might indicate underlying risks. Because often, schedule changes occur to keep an end date that is physically and mathematically impossible. If any real speed bumps are present in the schedule, a data analytics program will highlight them–assuming the program is utilized for the baseline schedule and every update.
2. Analyze Risks
Once you’ve identified your risks, examine each one closely. Consider the potential impact of each: the exposure, probability, timeframe, and classification. You can measure risk implications with the use of predictive analytics. By analyzing historical project data, you can predict future risks more accurately. For example, by analyzing schedule changes, you can see how they have historically impacted your project or led to increased risks.
3. Develop a Risk Response Plan
Developing a response plan involves deciding how to handle each identified risk – avoid, transfer, mitigate, or accept. Use data-driven insights to inform these decisions. For instance, if the data shows a recurring issue with a particular subcontractor, you might choose to mitigate that risk in the future by hiring a different sub. Similarly, if your data indicates consistent delays in a specific project phase, you might focus on what is making that phase so difficult to navigate.
4. Execute the Plan
Executing the plan involves prioritizing risks based on their impact and probability, often represented in a risk matrix. Utilizing specialized software, you can break down and visualize data for better access and understanding by all stakeholders. This step also involves developing contingency plans for risks that meet specific thresholds, guided by insights from both current and historical data analytics.
5. Monitor and Control Risks
Ongoing monitoring and control are crucial. As the project progresses, you should track existing risks and identify new ones, reclassifying risks as necessary. Creating regular reports keeps everyone informed. You also get ”bonus points” if you actively engage with real-time data, as it allows for the early detection of emerging risks, keeping your monitoring and control process up to date.
6. Measure Your Construction Risk Management Process Efficiency
Post-project analysis is vital for continuous improvement. Reviewing project data, updating overall risk metrics, and conducting risk audits can reveal areas for improvement. By conducting retrospective analysis, you can refine your risk management strategy over time, using historical data and experience to enhance future builds.
What specific technologies or software tools are recommended for analyzing construction schedule data effectively?
For analyzing construction schedule data automatically, companies can leverage advanced software tools designed for smarter construction risk management. Industry tools such as Oracle Primavera or Microsoft Project offer scheduling capabilities that SmartPM digests to offer continuous analysis for portfolio monitoring. We automate detailed risk assessments, and scenario analysis, and provide insights through data visualization, helping project managers to identify potential delays, cost overruns, and other risks before they impact the project.
The Benefits of Construction Risk Management
Efficient construction risk management leads to more successful project outcomes, reduced costs, and improved safety. However, this doesn’t happen by chance. It demands a thorough, organization-wide risk management strategy rooted in historical data review and the use of cutting-edge data visualization technologies, like SmartPM.
By embracing our data-driven approach to construction risk management, you can improve your understanding of risk at both the project and the organizational level. This not only bolsters immediate risk control but also significantly contributes to the long-term sustainability and success of projects and organizations.
Share