When you trust your critical path, you know what needs to be done to achieve your scheduled completion date. When you can’t, your project is at odds with itself. To trust your critical path, you need to trust your data – which starts with ensuring every last CPM construction schedule you create, analyze, review, or deliver is of a high enough quality to where performance can be analyzed.
While quality metrics or “indicators” vary from project to project, it’s important to remember that they are just that—indicators. Each project, with its unique characteristics and approaches, requires a customized strategy. However, a few key metrics should always be considered to maintain a reliable schedule, providing a flexible framework beyond the baseline.
How to Find the Risks in a CPM Schedule
One of the most important features of a CPM construction schedule is float. Float represents the flexibility in your project timeline. Specifically:
- Total Float: This is the amount of time an activity can be delayed without impacting the overall project completion date.
- Free Float: This tells us how long an activity can be delayed without affecting the start of subsequent tasks.
When float values are zero, it means there is no room for delay without affecting the project’s end date. The activities with zero float form what we call the critical path – the sequence of tasks that directly determine the project’s completion. These activities are non-negotiable; any delay here directly impacts project delivery.
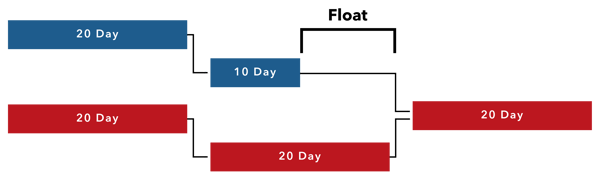
CPM construction schedules are designed to manage the complexity of large-scale projects with multiple stakeholders and dependencies. However, the integrity of your schedule – and your ability to meet project deadlines – relies on the accuracy of float values. If these values are unreliable, so is your critical path.
Not building schedules with best practices leads to confusion, making it difficult to distinguish between activities that are truly critical to the project’s end date and those that are not. This confusion can lead to delays, cost overruns, and mismanagement of resources.
To ensure that our schedules are both accurate and reliable, it’s essential to understand the primary risks that can compromise their quality. By addressing these risks head-on, we can make data-driven decisions that keep our projects on track.
Read on to explore the top three risk drivers of CPM construction schedule quality so you can make informed decisions:
#1: Have Zero Missing Logic in Your CPM Construction Schedule
There should be no missing logic in any schedule, no matter what kind of project it is. Every activity must have a predecessor and a successor. Unfortunately, this is also quite often an area of error. There are only two exceptions to this rule: two activities shouldn’t have a predecessor or a successor – the first activity because nothing precedes it, and the last activity.
In essence, every activity should have one thing before it and one thing after it; otherwise, the schedule is generally incomplete. It doesn’t matter as much about the types of logic you have, more so that logic is present throughout your schedule to avoid the risk of open-ended activities.
The Risk of Open-Ended Activities in CPM Construction Schedules
An activity without a predecessor or successor is what we refer to as an ‘open-ended’ activity. This term indicates that someone overlooked the necessary logic. Such activities pose a significant risk to your project’s schedule.
Open-ended activities are a risk issue because they will open up float even if the activity is a finish milestone. The more float opens, typically, the more compression happens. When this happens, you cannot trust your critical path.
#2: Minimize Long-Duration Activities in Your CPM Construction Schedule
According to the DCMA, no activity in your CPM construction schedule should exceed two months in duration. While I don’t necessarily agree with this blanket rule – there are specific activities, like procurement, that may naturally extend beyond two months (check out my article on How to Effectively Schedule Procurement Activities) – the underlying principle remains important.
This best practice aims to ensure that your schedule includes an appropriate level of detail. In essence, activities should be broken down into manageable, bite-sized pieces. As a general rule of thumb, a week’s duration is ideal, but try not to exceed a month. If necessary, keep activities under two months.
If you think about construction activities, specifically ones that have a long duration, it would be hard to gauge progress objectively. This is a risk because activities can be falsely labeled as critical or non-critical without an accurate progress calculation – once again, masking your true critical path.
#3: Be Mindful of the Overuse of Constraints in Your CPM Construction Schedule
The main problem with constraints is exactly what you might expect: they can mask the real critical path in your CPM construction schedule. By setting artificial start and end dates, constraints force multiple paths to seem critical when, in reality, they are not.
For example, if a “Finish No Later Than” constraint is applied, it might artificially make a non-critical activity appear critical, skewing the actual critical path. This can lead project teams to focus on the wrong activities, leading to inefficient resource allocation and potentially delaying the project.
On the other hand, hard constraints, like “Must Finish On” or “Must Start On,” can create an illusion that the project is on track, even if there are underlying delays. This happens because the constraints override the natural logic-driven sequencing of tasks. This false sense of security can cause project teams to overlook emerging risks or delays, as the constraints prevent them from seeing the true impact of issues on the overall schedule.
Best Practices to Manage Risks in CPM Construction Schedules
When issues like missing logic, long durations, and excessive constraints make their way into your project, it becomes harder to accurately track progress. The presence of these issues can make it unclear whether tasks are progressing on time due to effective management or simply because of schedule mismanagement.
To ensure your project maintains its schedule quality over time, use automated tools like SmartPM’s Schedule Quality Checker. Simply upload your schedule and uncover scheduling errors to avoid downstream risk with instant quality analysis, letting you know exactly what to fix before integrating updates into your project.
Visit our complete guide to construction risk management to learn strategies to identify, assess, and control risks for safer, more successful building projects.
If you’d like to learn more about how we can help you maintain schedule quality throughout the construction lifecycle, request a demo, and we’d be happy to show you how.