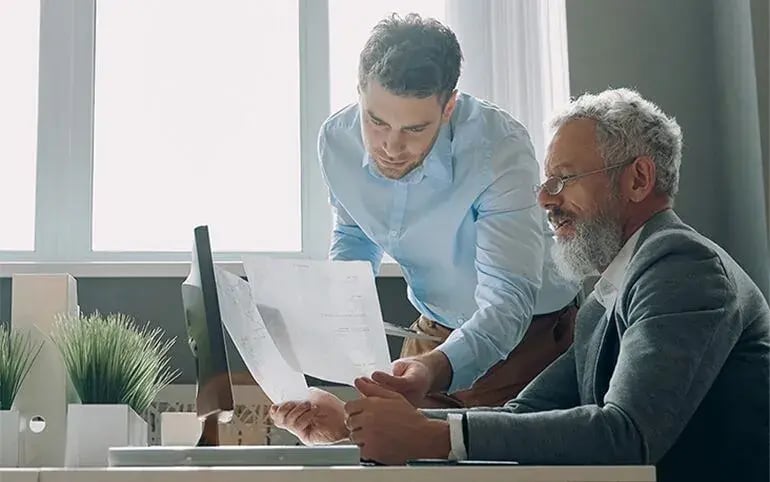
Blog
The DCMA 14 Checks: Schedule Quality Assessment
The DCMA guidelines are by no means perfect nor without controversy. But they help create quality schedules worthy of managing a job.

The Defense Contract Management Agency (DCMA) established guidelines in 2005 to improve scheduling practices as well as procedures to monitor and evaluate schedules. Later on, several revisions occurred, and out of this effort evolved a finalized 14-point Assessment Check used as a training course as well as a ‘framework for schedule quality controls. While not designed to become standard, this assessment, or what is commonly referred to now as the DCMA 14-point check, has been indirectly adopted by many industries, including the construction industry, as the standard protocol to evaluate the ‘quality’ of their project schedules.
However, the DCMA 14 is by no means perfect nor without controversy. Many take direct issue with several of the checks and the binary pass/fail grading system the methodology employs. (Please see check #6 -High float as an example.) Others don’t find some of them useful or valid and have elected not to include those specific metrics in their schedule quality assessments.
Schedule Logic
Logic describes the cause-and-effect relationship between tasks and their dependencies. In essence, it demonstrates how well tasks are linked together and defines how dynamic and flexible a schedule is.
The goal in project scheduling is not to manually enter hard start and stop dates (aka constraints) but to enter in durations and necessary logic. Durations and logic allow the software to calculate the start and stop dates for you. These dates, as well as start and stop times, are calculated relative to their predecessor and successors and adjusted by the scheduling software when changes and updates occur to the schedule.
- Predecessor: an activity/task whose start or finish controls the start or finish of another activity.
- Successor: an activity whose start or finish is controlled by another activity
However, predecessor and successor are not necessarily determined by the chronological sequential relationship of, let’s say, a ‘beginning’ task first followed by a second task in order. In fact, in a Start-to-Start relationship, both activities start at the same time. A predecessor, then, at its core, is an activity or event that controls. A successor is the activity being controlled. If, for example, we label two tasks as A and B, then we can understand how they relate to each other or the logic between them.
Finish-to-Start, Lag 0
There are 4 primary relationships between tasks, with ‘Finish-to Start’ being the most common:
- Start-to-Start: task B can not start until Task A has started (both tasks start at the same time).
- Start-to-Finish: task B can not finish until Task A starts (not common).
- Finish-to-Start: Task B can not start until Task A has finished.
- Finish-to-Finish: Task B can not finish until Task A has finished (both tasks finish at the same time).
Theoretically, in all four scenarios, each task has either a predecessor or a successor. And every relationship or logic tie has both. Remember, task A is the predecessor of task B. Task B is the successor of A. A perfect project schedule includes these logic ties on all activities, except the first and last.
The DCMA 14-Point Check: Explained
1. Missing Logic
The first DCMA guideline or check states that there can be no missing logic. This means that less than five percent (< 5%) of total tasks or activities in the schedule can have missing predecessors and/or successors or be ‘orphaned’ tasks.
As outlined by the DCMA guidelines, best practices indicate that missing predecessors and successors introduce risk into the schedule. This check ensures that no incomplete tasks adversely impact the project schedule. As SmartPM notes in their document Understanding your Schedule Quality Grade, “When an activity doesn’t have a predecessor, then it is likely constraint-driven; when an activity doesn’t have a successor, it will have a very high total float.” Additionally, it creates unrealistic float and absorbs hidden delays.
2. Leads (negative lag)
Although this seems the same as lag, this metric is the opposite of lag. And in fact, while lead and negative lag are used interchangeably, most of the construction industry uses the term ‘negative lag.’
Negative lag or a lead is defined as the number of days that a successor can start BEFORE a predecessor has finished. Essentially, this is the overlapping of two tasks and is generally frowned upon by most schedule guidelines.
The DCMA schedule quality lead check measures the percentage of tasks with a negative lag between them. The ideal number is zero. There should be no tasks with a negative lag between them. If a negative lag is found, then the schedule fails this metric.
Leads are often used to shorten the schedule. However, since this logic is predicated on 100% completion in the future of the predecessor, it introduces risk. The logic then supporting this DCMA metric is that the critical path and any subsequent analysis can be adversely affected by using leads.
Furthermore, the banning of negative lags is controversial. Caution is urged when rejecting negative lags as it may open up the owner to liability.
3. Lag
A lag is a waiting time or the interval between the completion of a predecessor and the start of its successor.
The DCMA lag check is more flexible than the leads check, and the DCMA is less disapproving of lag. It checks for the total number of tasks with predecessors with lag or positive lag. If more than five percent of tasks have lag, it is designated as failed.
4. Relationship Types
As stated previously, there are four primary relationship types. Of the four primary logical relationships between predecessor and successor in a project schedule, Finnish-to-Start relationships are the most common and considered the best logical ties between tasks. A good project schedule is filled mostly with FS relationships. In fact, the DCMA has designated that a large percentage — 90%— of total tasks should be comprised of the Finish-to-Start type. If at least 90% are FS (finish-to-start), then the schedule has passed this metric.
Why are FS relationship types considered the gold standard? Finish-to-start relationships provide logical flow in a schedule and, according to SmartPM, also eliminate the risk of trades working closely together.
That leaves 10% of tasks to account for. This 10% is allocated between two other relationship types:
- Start-to-Start
- Finish-to-Finish
The DCMA guide allocates < 5% for Start-to-Start in the schedule and 5% or less for Finish-to-Finish relationships. Again if more than 5% is found of either of these, the schedule fails this metric.
And last, the black sheep of the ‘scheduling logic ties family’ is the Start-to-Finish relationship which is seldom used. There is zero allocation by the DCMA of acceptable numbers permitted for the Start-to-Finish relationship.
5. Constraints
Schedule constraints are a no-no. Rather than let the program logic drive the start or end date of a given task or activity based on its relationship to other tasks, a schedule constraint artificially injects a HARD date into the schedule.
The DCMA has identified two forms of constraints labeled ‘hard’ and ‘soft.’ Hard constraints are defined as those dates defined as mandatory, for example, “Must Start,” versus soft constraints or those tasks that are flexible such as ‘Start No Earlier Than.’ The former clearly outlines a specific date that the task/work must start. The latter is more ambiguous and flexible and allows the schedule logic to drive it.
The DCMA is only prejudiced against those called hard or mandatory and only allows for five percent or less of total tasks to have a hard constraint assigned to a task. If a total number of hard constraints exceeds this threshold, then this check fails.
Hard constraints are considered negative in a schedule as they can create negative lag, override the schedule logic when updates occur, and prevent the schedule from being dynamic.
6. High Float
Schedule float is the total slack on a project schedule. It represents the total amount of time any task can be delayed before it delays the entire project or job.
44 is the magic number. High float is defined as forty-four working days or the equivalent of two months.
The DCMA guidelines dictate that five percent or less of total activities should not exceed forty-four working days of float. If more than five percent exceeds forty-four days, the schedule fails the high float test.
This metric is again a controversial one. Generally, having slack or ‘padding’ in a project is usually considered a good thing. As Ten Six Consulting notes, as long as your critical path is doing ok, a generous float can be something that project managers hope for. Furthermore, many argue that the guideline doesn’t take into account the length of the project and is defined the same for both a short 6-month project as well as a 2-year project.
Yet, others argue that having high float is still considered a sign of bad schedule quality according to the DCMA as it may indicate an ‘unstable network’ as well as missing logic (predecessors and successor relationships) and consequently obscuring hidden delays.
7. Negative Float
A negative float is defined as a task that has less than zero float —meaning that the task is delayed. It is a negative number representing the number of days of delay. If you are seeing a negative float, it means your schedule is already behind, and often that negative number is the amount of time you need to get the schedule back in line to hit the completion date.
DCMA is pretty cut and dry with this guideline. If any total tasks have a negative float, then it automatically awards a failed grade for this check. In other words, there is zero percent negative float allowed.
8. High Duration
The high duration metric checks that no task has an excessively high duration. It provides the ability to monitor and control the duration of tasks. A high duration for a task is generally considered to be no longer than two weeks. However, DCMA defines high duration as any duration that is greater than 44 working days again.
To arrive at a number, we divide the total number of high-duration tasks by the total number of tasks. To achieve a passing grade on the high duration check, five percent or less of total tasks should have durations of less than 44 working days.
The DCMA takes issue with high durations on tasks as it can be an indication of a lack of detail in the project schedule. I.e., Perhaps a task with a very long duration should be broken down into smaller tasks. Further, it increases the risk that the critical path can be disrupted.
9. Invalid Dates
This metric checks for invalid forecast dates and invalid actual dates as it relates to the data status date.
An invalid date is a task that has a forecast start/finish date in the past in relation to the data status date or, conversely, an actual start/finish date in the future after the project status date.
Per the DCMA, to have a high-quality schedule, there should be zero tasks that fall into this category.
10. Resources
This check requires that all tasks with durations of at least one day have resources allocated. This guideline is optional and does not have a pass-or-fail test. Specifically, each and every task should have at least one resource (labor, cost, or equipment) assigned to it for good project schedule quality. Resources are often missed, and it is critical to get accountability. For this reason, the DCMA has a zero percent threshold for any tasks without resources assigned to them.
11. Missed Tasks
The missed task check is a schedule performance test. Missed tasks are a good indicator of how well or how bad actual schedule performance is compared to the baseline schedule. It does not refer to tasks ‘missing’ from the schedule but those tasks that missed their finished dates and actually finished late. It is a key indicator of whether or not your project will finish on time.
Not simply a hard pass/fail measurement, if any are present, the DCMA guidelines now indicate a parameter of five percent missed tasks being within acceptable allowances.
12. Critical Path Test
This is a critical test that forces a ‘false’ critical path activity duration of 600 days to see then if the project completion date also extends out proportionally (600 days) as well. If it does not, it’s a major indication of a scheduling problem. This test is designed to identify broken schedule logic and missing predecessors and successors.
13. Critical Path Length Index (CPLI)
The Critical Path Length Index (CPLI) measures how feasible it is for a project to complete successfully and on time. The index is a calculation and involves using some acronyms such as CPL, which stands for ‘critical path length.’ The DCMA defines the CPL as the time in workdays from the current status date to ‘the end of the program’ or essentially the remaining project duration. The formula is as follows:
CPL (Critical Path Length) + Total Float
_____________________________________
CPL
The formula is a ratio and – for good schedule quality – should return a number that is greater than or equal to one. If the value is one, the scheduled completion date is realistic, and the project is on track. A value returned of 95% or less is considered a failure.
14. Baseline Execution Index (BEI)
The baseline execution index, or BEI, is another index attempting to measure a contractor’s performance and is a good early warning measure of a schedule’s quality. It measures the actual schedule performance against the baseline schedule. And like the CPLI, the returned value should be greater than or equal to one.
Studies indicate that if this check is performed, it can provide early detection of missed deadlines.
And there you have the DCMA 14 point Schedule Quality Assessment breakdown. Learning what these metrics and best practices are, as well as how to utilize them to improve schedule data integrity and performance, will greatly enhance your project. Most importantly, it will help you create excellent schedules of high quality that will pass the most rigorous of inspections and scrutiny, from project owner status updates all the way to full-blown audits.
Looking to keep your projects on track? Our construction scheduling guide covers the best methods, tools, and tips to help you improve efficiency and avoid costly delays.
Share