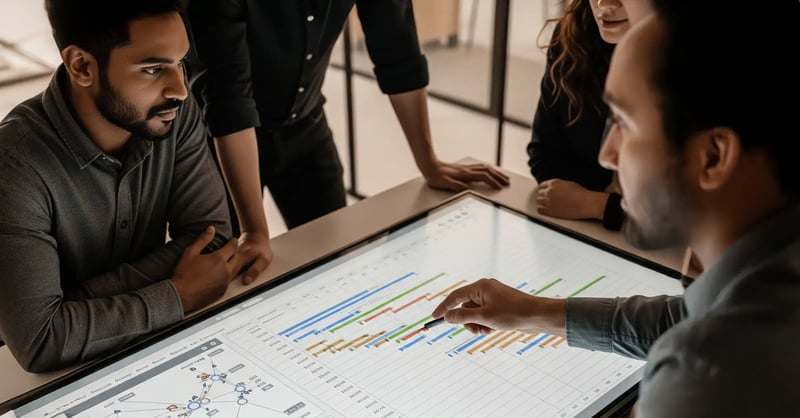
In the construction industry, even the most detailed plans fall apart without a strong schedule. Whether you’re managing a high-rise build or a residential remodel, your schedule drives the entire construction process.
In this guide, we break down the top 10 construction project schedule types, explain how they work, and offer practical examples to help you choose the right fit.
What is a Construction Schedule?
A construction schedule is a detailed plan that outlines the sequence, timing, and duration of project tasks and milestones. It serves as a roadmap for the project team, guaranteeing everyone understands what needs to happen, when, and in what order within a timeframe.
Why Construction Schedules Matter
Construction schedules do more than map out timelines. They’re the strategic backbone of every successful project.
Here’s why a strong construction schedule matters:
- Improves Project Visibility: A detailed schedule gives teams and stakeholders a clear view of project scope, sequence, and timing. It helps spot potential delays early, before they become problems, and ensures everyone is aligned on priorities and deadlines.
- Boosts Accountability and Coordination: With clearly assigned tasks and timelines, schedules hold teams accountable and minimize gaps between handoffs. When everyone knows what’s expected and when, coordination between trades becomes smoother and more efficient.
- Supports Resource Optimization: Labor, equipment, and materials are finite and expensive. A good schedule ensures resources are allocated where they’re needed most, minimizing idle time and preventing overbooking.
- Enables Proactive Risk Management: Schedules make it easier to identify critical paths, track float, and run what-if scenarios. This approach helps construction project managers anticipate and mitigate risk before it derails the build, minimizing unexpected disruptions.
- Drives Data-Driven Decisions: The best schedules evolve over time. With regular updates and historical comparisons, schedules become a powerful tool for tracking progress, measuring performance, and forecasting outcomes with greater accuracy.
- Strengthens Stakeholder Communication: From subcontractors to owners, clear communication is key. Schedules distill complex timelines into digestible formats that help stakeholders understand project status and stay engaged without getting lost in the details.
In short, a construction schedule isn’t just a plan but also a management tool. And when used effectively, it turns uncertainty into control, chaos into clarity, and good intentions into on-time, on-budget delivery.
Top 10 Construction Schedule Types
Here are the most commonly used construction schedule formats, each with unique strengths depending on project scope and complexity:
1. Critical Path Method (CPM)
Overview: The Critical Path Method (CPM) is a project modeling technique widely used in construction management to identify the most critical activities in a project timeline. It identifies the longest sequence of dependent activities (known as the “critical path”) that determines the shortest time in which a project can be completed.
CPM not only highlights these non-negotiable activities but also indicates which activities have “float,” providing flexibility to start or finish later without affecting the project’s end date. This makes CPM a powerful tool for managing risks, optimizing resources, and maintaining control over schedule performance.
Use Case: Used in commercial buildings, infrastructure, and heavy industrial projects – any project with interdependencies and tight deadlines.
Example: In the construction of a hospital, CPM might show that the structural steel installation can’t begin until the concrete core is complete. If the concrete is delayed, steel and every subsequent trade will be delayed too. This early warning helps project managers take action and stay on track.
2. Gantt Chart
Overview: A Gantt chart is a time-based bar chart used to illustrate a project schedule. Each activity is represented as a horizontal bar, with its length indicating the duration of the task. Gantt charts provide a clear visual representation of project timelines, task sequences, overlaps, and dependencies.
While a Gantt chart alone doesn’t calculate the critical path or float, it becomes a powerful communication tool when generated from a CPM schedule. With CPM, activities can be grouped by phase or responsibility, and project milestones can be highlighted to track key deliverables.
This helps translate complex data into a format that’s easier to understand for clients, stakeholders, and field teams.
Use Case: Best for stakeholder presentations and high-level overviews.
Example: A residential contractor might use a Gantt chart to show when framing, electrical, and plumbing tasks will begin and end, helping clients see how everything fits together.
3. Program Evaluation and Review Technique (PERT)
Overview: The Program Evaluation and Review Technique (PERT) is a scheduling method that uses probabilistic time estimates to predict project duration more accurately under uncertainty.
Unlike deterministic approaches, PERT requires three time estimates for each activity: the optimistic (O), most likely (M), and pessimistic (P) durations. These are then used to calculate an expected duration using a weighted average formula: (O + 4M + P) / 6, giving a more reliable estimate of the amount of time each task may require.
PERT is especially useful during the planning phase of projects that involve innovation, complex logistics, or external dependencies, allowing teams to identify potential risks and buffer time accordingly.
Use Case: Suited for uncertain or research-heavy construction projects.
Example: A design-build firm might apply PERT for a new public park project where permitting times and environmental factors are unpredictable.
4. Line of Balance (LOB)
Overview: The Line of Balance (LOB) is a specialized scheduling technique used for projects with repetitive tasks across multiple units or sections. It visually maps the sequence of work for each trade across these units, ensuring continuous workflow and optimal crew utilization.
The key benefit of LOB is its ability to highlight production imbalances, allowing teams to adjust crew deployment and prevent bottlenecks. It's especially effective in projects like hotels, apartment complexes, or office towers where the same scope of work is repeated on each floor or unit.
Use Case: Common in high-rise construction or multi-unit developments.
Example: In a 10-story apartment build, LOB ensures that as soon as one crew finishes electrical on the third floor, another starts plumbing on the same floor, keeping the work flowing smoothly.
5. Q Scheduling (Quantitative Scheduling)
Overview: Q Scheduling is a method that focuses on managing the quantities of work rather than time alone. It integrates schedule and resource planning by visually linking the amount of work (such as cubic yards of concrete or square feet of drywall) with the time and location where it will be installed.
This technique is especially useful for projects involving repetitive tasks across linear or large geographic areas, such as roads, pipelines, or tunnels. Q Scheduling helps detect spatial conflicts, optimize resource allocation, and prevent task overlap by visualizing production rates and sequences in a more intuitive way.
Use Case: Ideal for highway or pipeline construction.
Example: On a highway project, Q Scheduling maps the amount of asphalt laid per day against crew availability and material delivery schedules.
6. Last Planner System (LPS)
Overview: The Last Planner System (LPS) is a lean construction management method that focuses on improving planning reliability and workflow by engaging those closest to the work—"last planners" such as superintendents, foremen, and trade leads.
It operates on the principle of collaborative planning, where short-term commitments are made based on actual site conditions, resource availability, and team consensus. LPS includes several components: master scheduling, phase planning, look-ahead planning, weekly work planning, and daily huddles.
This system not only increases accountability but also fosters continuous improvement through constraint analysis and performance feedback.
Use Case: Useful in projects where changes are frequent.
Example: A renovation project with variable site conditions might use LPS to adapt weekly tasks based on recent developments and team input.
7. Fast-Tracking
Overview: Fast-tracking is a schedule compression technique where project phases or activities that are normally done in sequence are performed simultaneously to compress the overall schedule. This approach can significantly reduce overall project timelines but comes with increased risk of coordination issues, rework, and communication breakdowns.
Effective fast-tracking requires careful planning to identify activities that can start based on partial or preliminary information without jeopardizing the project’s integrity. It demands strong collaboration among trades, detailed sequencing, and proactive risk mitigation to avoid delays later on.
Use Case: Suitable for projects with tight deadlines and overlapping scopes.
Example: Starting interior finishes before structural inspections are complete to accelerate delivery, though this raises coordination and risk challenges.
8. Milestone Chart
Overview: A Milestone Chart is a high-level project scheduling tool that highlights significant events or decision points throughout the construction lifecycle. Rather than detailing every task, it focuses on key achievements such as permit approvals, inspections, or handovers that mark progress and signal readiness for the next phase.
Milestone charts are ideal for status reporting, stakeholder meetings, and early project planning because they simplify communication while maintaining visibility of major targets. However, they should be supplemented with more granular schedules to manage day-to-day operations.
Use Case: Good for communicating progress to non-technical stakeholders.
Example: A project owner might track five major milestones: design complete, permits approved, foundation complete, TCO (temporary certificate of occupancy), and final handover.
9. Resource-Oriented Scheduling
Overview: Resource-Oriented Scheduling is a technique focused on the best allocation and utilization of key project resources such as labor, equipment, and materials. Instead of scheduling purely by task sequence, this method ensures that resources are not over-committed and are available where and when they are needed.
It is particularly useful in environments where multiple projects or trades share the same resources. Resource leveling (resolving over-allocations by adjusting task timing) and smoothing (balancing workloads without changing the project end date) are often used to avoid conflicts and ensure crews and equipment are used efficiently.
This approach helps avoid delays due to shortages, reduces idle time, and supports more predictable project execution through better resource management.
Use Case: Effective in labor-intensive projects or when subcontractors are shared.
Example: On a warehouse project, this schedule ensures electricians and plumbers are not double-booked or left idle, maximizing labor productivity.
10. Calendar Scheduling
Overview: Calendar Scheduling is one of the simplest and most accessible scheduling methods, often built using basic tools like Excel, Google Calendar, or a whiteboard. It assigns tasks to specific calendar dates, helping teams visualize what needs to happen each day or week.
This method works well for small-scale or short-duration projects with clearly defined scopes, limited dependencies, and few trades. Its strength lies in its ease of use and quick setup, but it lacks the flexibility and depth of more advanced systems, making it less suitable for large or complex jobs with frequent changes or coordination needs.
Use Case: Works best for smaller, predictable projects.
Example: A general contractor managing a kitchen remodel might list all tasks on a monthly calendar for straightforward tracking.
Construction Schedule Types – Quick Comparison
Schedule Type |
Best Use Case |
Complexity Level |
Ideal Project Size |
Critical Path Method (CPM) |
Managing task dependencies and timelines in detail |
Medium |
Large, complex builds |
Gantt Chart |
Visualizing task durations and overlaps |
Low–Medium |
Small to medium projects |
PERT |
Planning with uncertainty and estimating time ranges |
Medium–High |
Innovative or high-risk projects |
Line of Balance (LOB) |
Coordinating repetitive tasks across multiple units |
Medium |
Multi-unit, high-rise |
Q Scheduling |
Managing production rates across linear scopes |
High |
Infrastructure, linear projects |
Last Planner System (LPS) |
Improving planning reliability with team input |
Medium |
Dynamic or renovation projects |
Fast-Tracking |
Compressing project timelines by overlapping phases |
Medium |
Schedule-driven projects |
Milestone Chart |
Highlighting key events and stakeholder alignment |
Low |
All sizes (for communication) |
Resource-Oriented |
Optimizing labor and equipment across tasks/projects |
Medium–High |
Labor- or resource-constrained projects |
Calendar Scheduling |
Simple date-based planning with minimal dependencies |
Low |
Small, short-duration builds |
How to Choose the Right Construction Schedule Type
Selecting the most effective scheduling technique depends on a mix of project-specific factors. Here’s how to decide:
- Project size and complexity: CPM suits large-scale builds, while Gantt charts may suffice for smaller jobs.
- Team experience: LPS works best with collaborative, experienced teams.
- Stakeholder needs: Consider communication clarity and level of detail required.
- Resource constraints: Use resource-based methods if labor or material availability is a challenge.
A hybrid approach is often best—pairing, for example, CPM with Gantt charts for both strategic oversight and stakeholder updates.
Common Mistakes to Avoid
Even the best schedule can fail without proper execution. Avoid these pitfalls:
Neglecting schedule updates: Stale data leads to poor decisions. Regular updates ensure teams are working with the most accurate and relevant information.
Overlooking float: Mismanaging float can turn minor delays into critical project delays. Understand and monitor float to maintain schedule flexibility.
Underestimating task durations: Leads to frequent schedule revisions and potential cost overruns. Use historical data and expert judgment to set realistic durations.
Ignoring crew workflows: Mismatched labor sequencing reduces efficiency. Plan sequences to align with trade availability and work continuity.
Failing to integrate resource planning: Resource bottlenecks can derail timelines. Incorporate labor, equipment, and material availability into your schedule.
Overcomplicating the schedule: Too much detail can blur critical information. Keep schedules aligned to the baseline while allowing flexibility for realistic field conditions.
Lack of stakeholder engagement: Failure to align with owners, subcontractors, and team members can cause misunderstandings. Involve all key players in schedule development and updates.
Final Thoughts
Understanding the types of construction schedules is key to selecting the right tool for your project. By matching the method to your project's demands and avoiding common missteps, you set your entire project up for success.
For a deeper dive into construction scheduling tools, methods, and best practices, check out our comprehensive guide to construction scheduling.
To see how SmartPM helps streamline and strengthen construction schedules with real-time analytics and schedule intelligence, explore our platform or book a demo today.
Frequently Asked Questions
-
The Critical Path Method (CPM) is the most widely used because it provides a detailed view of task dependencies and helps project managers identify which delays will impact the completion date.
-
Yes. Many construction teams combine scheduling types, such as using CPM for detailed planning and Gantt charts for stakeholder updates, to improve clarity and execution.
-
Gantt charts or calendar scheduling are ideal for smaller, less complex projects. They’re easy to use, visually intuitive, and don’t require advanced scheduling software.
-
Regularly—ideally weekly or bi-weekly. Timely updates ensure decisions are made using current data, keeping the project on track and stakeholders informed.
-
SmartPM provides real-time schedule analysis, risk insights, and performance tracking. It helps teams make data-driven decisions and spot issues before they become delays.
-
Float shows how much flexibility you have before a task delays the project. Managing float properly helps maintain momentum and adapt to changes without impacting delivery dates.
Share
- Share Top 10 Types of Construction Schedules Explained (With Examples) on Facebook
- Share Top 10 Types of Construction Schedules Explained (With Examples) on LinkedIn
- Share Top 10 Types of Construction Schedules Explained (With Examples) on X (Twitter)
- Share Top 10 Types of Construction Schedules Explained (With Examples) via Email