Project controls are the data gathering, data management, and analytical processes used to predict, understand, and constructively influence the time and cost outcomes of a construction project or program by communicating information in formats that assist effective management and decision-making. In other words, project controls are analytical processes and outputs used to understand and communicate project information.
While some believe that project controls live within a department, they don’t. They are a mindset that should make up the fabric of a construction organization to support overall project management.
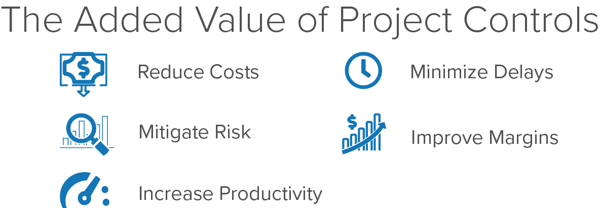
The Construction Industry Institute helps emphasize that project control systems are an important part of the overall project management effort. They support the achievement of project objectives. In other words, project controls streamline efficiency by exposing and highlighting risk or mismanagement through the key metrics.
Therefore, project controls allow for performance measurement with planning metrics and checkpoints to ensure standards are met. Even though the seeing the benefits involves a relatively simple process, project controls continue to be underutilized in the construction industry.
The Challenge with Project Controls
It is very fair to state that, in commercial construction, project controls aren’t a top priority for a large percentage of construction companies. For many, contingency budgets and padding the schedule are the extent of their “project controls.
I know this because I’ve analyzed thousands of commercial construction projects. Here are some important takeaways:
- <4% of General Contractors have a dedicated project controls team and/or process in place on their projects.
- The only companies investing in and embraced project controls reside in the upper half of the ENR’s top 400 CM firms.
- Many Commercial Construction Companies in the United States leverage project management tools. However, they do not invest much in any project control functions.
- The lack of project controls contributes to significant overruns, delays, and disputes.
SmartPM Analyzed Over 50,000 Schedules and Found:
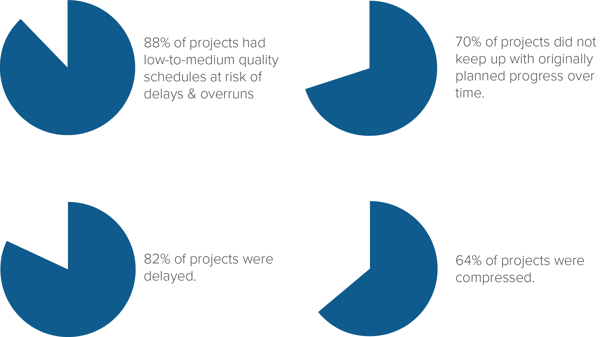
This poses yet another unfortunate reality: the lack of project controls has a great effect on the global economy and the environment. According to McKinsey, the construction industry wastes $1.6 trillion dollars annually in overspending, usually resulting from project mismanagement, delays, and overruns.
Take a moment to imagine the potential of what almost two trillion dollars could have been spent on every year…
A Broken Record
If hearing “construction delays & overruns” sounds like a broken record, it’s because it is. It’s what every technology claims to solve. Project management systems, mobile apps, BIM, drones, and document control tech all claim to help eliminate delays and overruns. But if the goal is to systematically optimize construction, project controls are the only real answer.
The reality is that delays and overruns have the ability to be negated wholly through analytics designed to support project controls. Project controls provide ample opportunity to fix these issues, but the answer is at the crossroads of “Project Controls” and “Technology.”
Key Schedule Control Metrics
Any given construction project has a world of data behind it, which controls help bring to light. As mentioned above, there are many different avenues to achieve an effective process, but here are five schedule controls we believe to be most helpful in delivering the highest quality project:
- Schedule Quality- is an assessment of how well a schedule is built and whether or not best practices are incorporated.
- Earned Value Analysis (EVA)- measures a project’s cumulative progress at any given point. This serves as an early warning sign for potential progress challenges.
- Critical Path Delay and Recovery- tracks the number of days that have been delayed due to impacts on the critical path. Recovery entails the processes and changes made to overcome critical path delays.
- Compression- is a gauge of how much work is being fit into the remainder of the project duration and how that work compares to the plan.
- Forecasting- utilizes historical performance to predict future end dates of key milestones.
The metrics above track actual insights by assessing activities required against budget or volume of material. But how do you begin using project controls as part of your daily practices? This is a tall order; definitely easier said than done.
Using Automation
The easiest way to control project outcomes to have controls around your processes that allow all stakeholders quickly gain access to project health data in ways they never have before. Imagine having an eye on subcontractor performance, risk, impacts, delays, inefficiencies, predictions, etc… The result? Objective, fact-based decisions.
Furthermore, the metrics offered by automated project controls have a lot to offer the construction industry, such as:
- Reduce costs- using Key Performance Indicators (KPIs) reduces the overall cost of projects by allowing critical decisions to be made quickly.
- Increase Productivity– effectively manage team members by providing checks and balances on project activities.
- Higher visibility– project controls allow team members across the board to be up to date on the construction schedule.
- Mitigate Risk– implementing mitigation strategies allows risks to be avoided, accepted, reduced, or transferred.
- Improve Margins- by optimizing construction schedules properly, many projects are able to finish under budget by executing best planning and actual practices.
By using an automated process, like SmartPM’s schedule controls platform, more visibility into actual project processes becomes clear. Additionally, critical decisions concerning end dates and budgets have the accurate data to back them up.