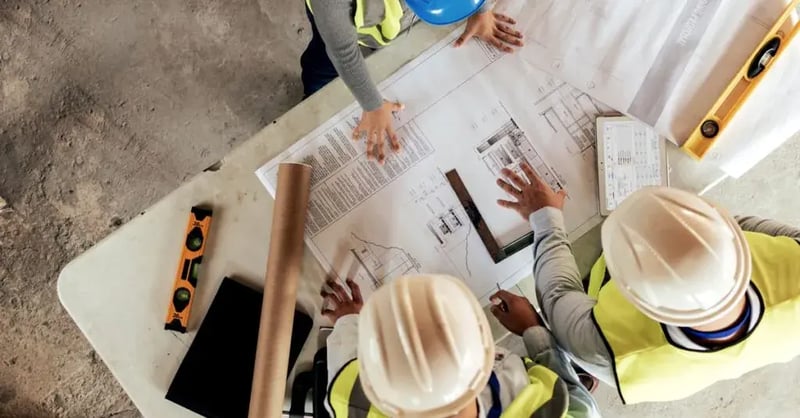
Blog
Forensic Delay Analysis is Archaic in Construction
Forensic delay analysis is commonly used in construction to investigate the causes and impacts of delays during the project lifecycle.

Throwing hundreds, if not thousands, of people with different roles (architects, engineers, subcontractors, owners, superintendents, etc.) alongside materials and equipment and then having to decide where everyone and everything should go (on top of having to make the normal decisions outside of work) is a recipe for forensic delay analysis.
The more you have to decide based on gut instinct alone translates into bad decisions, the further along you are in your day. Have you ever gotten home from work and wondered why you did something? Or, my personal favorite, going to the grocery store after a long day, getting many things you don’t necessarily need, and forgetting the one thing you actually do?
This process all comes down to gut instinct and intuition. While intuition can be a strong force, intuitive decisions can be grounded in heuristics, which help us screen out large amounts of information, thereby limiting the amount that needs to be processed. This is fine and dandy when it comes to less consequential matters. But, if you are dealing with a multi-million or billion-dollar project, you should combine that intuition with something more powerful.
That something is data.
How is Data Utilized in Construction?
As noted in the Business Insights Blog from Harvard Business School Online, while intuition can anticipate a sequence of events, data is what helps you verify, understand, and quantify. However, despite the latest estimates positing that over 328 million terabytes of data are created daily, the construction industry does not utilize its data to its fullest potential.
In fact, according to FMI, 95% of all construction industry data goes unused. Moreover, it’s estimated that 13% of construction teams’ time is spent looking for the right data to keep their projects progressing, which is unfortunate as the best data to arm your team with is real-time data. Your teams should not be expected to sift through piles of numbers, photos, Excel sheets, and emails months or even years after the project is finished. Nor should they be held responsible for inadequate data processes.
Before founding SmartPM, I spent my days doing that exact thing: poring over schedule files to find data. However, I tended to this task after the project was finished–late and over budget, of course–and in the middle of the resulting claim and dispute process.
What is Forensic Delay Analysis?
Forensic delay analysis is commonly used in construction to investigate the causes and impacts of delays during the project lifecycle. It involves performing detailed data analysis of a project’s CPM schedule data, as well as investigating the events and circumstances that contributed to the delay.
This type of analysis determines the root causes of delay and assigns responsibility for them to resolve disputes and prevent future ones from happening. The downside of forensic delay analysis is the accumulation of an abundance of additional costs related to lawyers, consultants, interest, and other management and operational costs, depending on the type of forensic delay analysis used.
Types of Forensic Delay Analysis
There are several types of forensic delay analysis commonly used in the industry:
- Impacted As-Planned
- Collapsed As-Built
- As-Planned vs. As-Built
- Time Impact Analysis (TIA)
- Windows Analysis
While each technique “finds the root cause of delay,” it is essential to note that different methods produce different results. This means that each type of analysis has its limitations, which are summarized below.1
Limitations in Impacted As-Planned Forensic Analysis
- Theoretical assumptions make the usefulness of the approach questionable
- Cannot account for changes in activity logic or duration
- Results are based on hypothetical scenarios
- Cannot identify actual concurrent delay
The Challenges of Collapsed-As-Built (CAB) Forensic Analysis
- Time-consuming
- As-Built logic is subjective
- Does not Calculate delay based on the contractor’s contemporaneous intentions
- Cannot distinguish pacing activities from critical delays
- Can only identify compensable delay periods, not critical paths
- Requires many subjective assumptions
Drawbacks in As-Planned vs. As-Built (APAB) Forensic Analysis
- The As-Built sequence must relate to the As-Planned sequence for the activity level variance method
- Cannot deduce the As-Built critical path without monthly progress updates
- Creating a proper As-Built program can be expensive and resource-intensive
Critiques of Time Impact Analysis (TIA) Forensic Analysis
- Results are based on hypothetical scenarios
- Cannot identify actual concurrent delay
- Labor-intensive and technically complex
- Requires frequently prepared progress schedules
Weaknesses of Time Impact Analysis (TIA) Forensic Analysis
- Correctly updated progress programs are required
- Activity start, finish, and float constraints may create gaps in the critical path
- Logical errors in early schedule updates that were corrected in later updates present inaccurate results
- Requires planning expertise
The Inefficiency of Forensic Analysis
As shown above, any forensic delay analysis technique requires a thorough understanding of project schedule files and the data held within them. More importantly, it requires access to accurate, valid data – meaning, if the schedule files lack well-grounded, rational logic, then the analysis risks being unreliable and not credible.
In Pacific Construction Co. Ltd vs. Greater Vancouver Regional Hospital District1, the British Columbian Supreme Court held that forensic delay analysis requires a valid and reasonable baseline schedule. They found that the contractor’s baseline schedule was inadequate and failed to represent the project’s scope. Therefore, the court used the owner’s design changes to determine the cause of the delay.
Forensic delay analysis is not solving the problem if the industry uses less than 95% of its data and most projects are delayed, rendering it outdated and inefficient because it focuses on investigating the past. And, if parties disagree and do not have the data to perform an objective analysis, the process is dubious, at best.
The Solution: Utilizing Data Effectively
The most important thing you can do to utilize your data more effectively is to implement a proactive approach to project management, focusing on preventing delays and overruns at the outset.
Luckily, most projects require a CPM schedule to be created and maintained per the contract. CPM schedule files are the only data set in construction that lists all the activities needed to complete a project, from start to finish, while also explaining the interdependencies among those activities.
However, as noted above, the industry struggles with creating and maintaining high-quality schedules. This is an issue as low-quality schedule data is useless. Beginning with a high-quality baseline schedule requires a high level of detail, as a comprehensive plan helps identify potential problems and risks before the project starts.
From there, choose a project management software. Many construction companies already leveraging software to assist with schedule management. I recommend choosing one that allows for real-time updates and analysis of project progress so that you recieve a comprehensive view of your project’s status, identify potential issues early on, and take the necessary steps to avoid them from happening.
Leveraging a cloud-based project management software has several advantages, such as:
- Easy access
- Cost-effectiveness
- Low maintenance technology
- Improved team productivity
- Time savings
Most importantly, the effective use of schedule data fosters open communication with all project parties. Everyone from the C-suite to the site teams must accurately understand the project. This includes understanding the risks and what the data says for the best results.
An easy way to do this is to present data in formats that are easy to understand. In other words, utilize data visualization.
What is Data Visualization?
Data visualization is data representation through graphics, such as charts, plots, infographics, and animations. Using visual displays of information assists with communicating complex data relationships. Additionally, you can visualize data-driven insights in a way that is easy to understand.
Data visualization has several benefits, including:
- Enabling understanding of a large amount of data at a glance
- Increasing the speed of decision-making with real-time information
- Identifying errors in data sets
What Are the Risks of Utilizing More Data in Construction?
While the benefits of utilizing data are vast, some key risk factors make users wary about leveraging cloud-based software. For one, security issues are top-of-mind for many construction companies. If project data falls into the wrong hands, the consequences might be more substantial than the delays and overruns companies usually experience.
Another concern is the insights given by utilizing data. The age-old adage, “garbage-in, garbage-out,” attests to this issue. Essentially, the quality of insights is only as good as the quality of data they came from. A prerequisite for generating accurate, valuable data is regularly updating and reviewing the schedule with all involved parties.
Schedule updates are a point of adhesion for many projects. However, leverage software that pinpoints and uses checks and balances to ensure your updates are feasible and trustworthy. Your updates provide instrumental data for risk mitigation, better communication, and harmonious project outcomes.
As noted by Sir Michael Latham in Constructing the Team, risk can be managed, minimized, shared, transferred, or accepted but cannot be ignored. However, utilizing your schedule data identifies and mitigates potential project risks. Using schedule data in this way minimizes the need for forensic delay analysis.
Why Forensic Analysis is Archaic in Construction
If the majority of data goes unused in the construction industry; the majority of projects end up late and over budget; and project managers experience a high amount of decision fatigue; then there has to be a better process for accurate decision-making that leverages data for better project results.
The well-known process of forensic delay analysis has served its purpose. The techniques can determine the cause of delay but are ultimately subjective and are used after the fact.
By utilizing real-time data and visualization, construction companies can proactively get their projects in line. This includes more alignment with contracts, resulting in objective decisions that benefit all parties involved.
Share