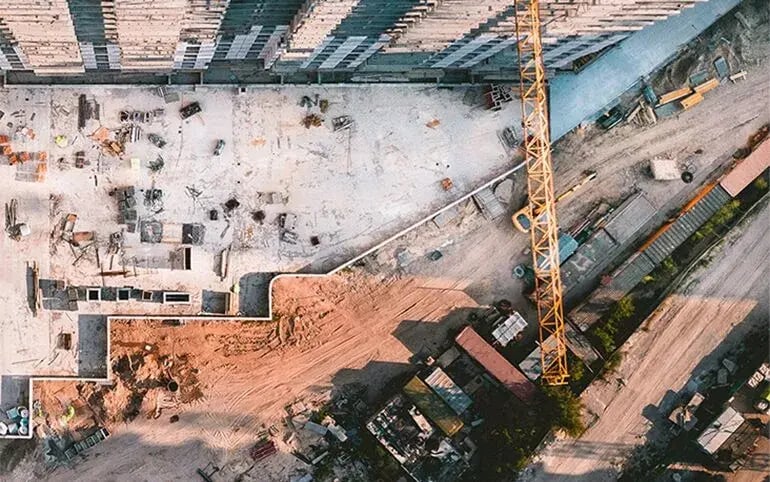
Blog
CPM Scheduling Basics
Critical Path Method (CPM) Scheduling has been around for over half a century. However, it’s often not utilized to its full potential or its original promise.

CPM Scheduling basics are rarely ever taught. I’ve frequently seen many project teams turn to planning and scheduling using their most comfortable methods. Yet, as familiar as these methods might be, they do not have the same capabilities as scheduling software.
When you first start using CPM scheduling, it’s normal to feel overwhelmed trying to incorporate realistic numbers and expectations. You don’t want to disappoint your clients. But, at the same time, you need to be honest about what you need to complete the project, whether it’s more time or more resources.
Understanding how to manage a construction project using the Critical Path Method takes some time. However, its success has been proven time and time again. In this blog, I’ll explain why it’s a great tool to have at your disposal in the construction industry.
Where Does CPM Scheduling Come From?
Consider an example from over a century ago, before computers. Schedules were manually represented as bar charts, including a list of tasks with their durations, all arranged over time. Despite lacking logical connections, each task had a start and end point. Today’s Critical Path Method (CPM) scheduling mirrors this approach, aligning with our natural thought process by visually showing tasks, durations, and logical sequences.
Essentially, when envisioning the building process, humans have always had to consider the following questions:
- How will the structure be built over time?
- When one activity finishes, which one can begin next?
If you think about it, it is fascinating how the human mind functions when building a project–laying out items over time with dependencies and knowing that certain things need to happen before others begin. If you’re in construction and looking at a design, you probably think about order.
For example, you can only lay a foundation once you dig a hole. Once that foundation is laid, you can begin laying out each floor. Once the floors start going up, you can begin working within each floor and have it all mapped out in your brain.
The Beginning of CPM Scheduling
Luckily, in 1957 CPM scheduling came to fruition with computers. The program highlighted critical activities for ideal project progress and performance. Most importantly, the computer highlighted the path that is most critical toward a completion date based on where the project stood at a certain point in time.
Then, by the 1980s, Oracle introduced Primavera, the first DOS-based CPM scheduling program. If used correctly and made available to everyone in construction, projects should get done on budget and on time every time ground is broken.
CPM Scheduling Basics
CPM scheduling is a quantitative approach to demonstrating workflow using network diagrams. It is a methodology designed to assist in managing complex projects using an algorithm to generate a Gantt chart (schedule) based on user entry of all anticipated discrete work activities and the relationships between them.
Understanding the methodology behind CPM scheduling is crucial so that the program can do what it is designed to do. The agenda behind CPM prioritizes work activities based on their potential for delaying key milestones and the project’s end date. The best thing about it is that you do not need to do the math; the program does the math for you so that you can instantaneously know the high-priority areas for today to manage towards an end-date years later.
The Importance of Determining High-Priority Areas
To know how priority is determined and what activities need to be completed before others, CPM programs create a calculation called float (or slack). Float is the number of days an activity can be delayed before it impacts the project’s end date. It enables project teams to prioritize resources and highlights the most “critical” path toward achieving the end date as well.
The critical path (highlighted in red), or the longest path, is the path that extends from the current date until the end date with no room for delay. Without it, you do not have the information you need to make crucial decisions regarding common construction challenges, such as resource constraints.
The Importance of Knowing CPM Scheduling Basics
CPM was created to assist in the effective management of resources to complete projects on time and within budget. It is not for claims nor to keep stakeholders happy; it is simply designed to manage jobs effectively.
The challenge is that many project schedules are of low quality. Over the past couple of years, we’ve compiled over 20,000 project schedules across the industry and noticed that about 80% or more are of medium to high risk of being useless, meaning they are not built using best practices. What does this mean? Well, there is likely a lack of understanding of best practices, meaning many people do not realize why CPM is needed in construction.
Why is CPM needed in Construction?
1. Construction is complex.
I may be biased, but I do not think any other task in the world is more complex than building a construction project–or, at least, not very many. If you think about the projects being built and their time frames, it usually takes many years to build something that costs billions of dollars.
Plus, there are typically hundreds of people on site with materials coming in from all over the world; using a design that may or may not be complete; doing things that look good on paper but do not fit in a three-dimensional world; and weather concerns, change orders, and RFIs. All these things are happening at once and are kept on a timeline. This is a lot to keep track of, and you need to know where to place everything on-site to manage that timeline.
2. Things rarely, if ever, go “as planned” in construction.
Consider what is possible: for example, how long it should take to install drywall, concrete, windows across various locations, etc., alongside design, weather, labor, and supply chain issues. With all the moving parts happening on the job site, even the most coordinated plan cannot guarantee that everything will go as planned.
When setting durations, most people have an optimism bias or planning fallacy. Everyone I know is guilty of it; it is how our brain is wired–to think about the quickest way to get something done. So, naturally, the construction industry is challenged in this regard. But, in reality, all the project risks listed above have been in play since the first construction project; they didn’t just appear overnight. This means that all these things take longer, and then the impacts compound.
Knowing that nothing ever goes as planned–and projects are complex, to begin with–is the reason why we want to use a tool like a CPM scheduling engine.
3. Delays are costly (to all parties).
When you say something is going to get done in a certain amount of time, budgets are aligned based on that date. Cost estimates are created for X number of people in these trailers with this equipment. But, if it takes months longer, the costs have not been accounted for and subsequently become overruns.
Let’s say you are building an asset for an owner. The owner wants that asset built for a reason, usually for some sort of financial gain. Whether it be leasing out apartments or building a manufacturing facility, it is a product that is going to be delivered. So, the owner’s finances depend on that delivery. And when it is not delivered, the losses can come in the form of both increased costs and lost revenue generation–making delays a costly problem.
Furthermore, if the problem results in a dispute, there are additional costs associated with lawyers and consultants, probably the most expensive personnel to have on a construction project.
4. Scheduling helps out in a big way.
High-quality schedules help projects get done on time and within budget because they allow for communication and collaboration throughout the project lifecycle. I view them as one of the most powerful tools in construction but also the least understood. If we can merge the worlds of understanding and utilizing schedules the way they were designed, there will be better outcomes for the construction industry.
How Does CPM Scheduling Work?
- It lists all tasks necessary to complete a construction project.
- Durations are assigned to each task.
- Relationships are assigned among the tasks to create order.
- This order is superimposed on a calendar to create a readable plan.
- Priority is assigned to each task based on its sensitivity to delaying the project end date.
The resulting calculation helps you prioritize activities based on criticality, allowing you to decide who will be working on what activities today. I’ll give you an example visually.
This is a project I worked on, a college dorm with five buildings wrapped around a parking garage. The demo needed to happen, then the excavation, then we could start the parking foundation. Once the parking foundation was done–which was in the middle of the site–we could start putting down the foundations for all the other buildings. Once each foundation was laid, we could put in framing, enclosures, etc.
What is most important here is the critical path. The one in red extends from the beginning of the job to the end of the job, such that if anything on this path is delayed, it delays the end date of the job. For instance, if the parking foundation were delayed for a month, the end date would also push out a month.
The areas not on the critical path are not critical but are also important; they have room for delay. So, if there were not enough resources working on the job at any point, other activities could get done in the meantime. But, the critical path is where your focus needs to be because it is where your resources are needed most.
The Most Important Rule of CPM Scheduling
It is important that the critical path is accurate, or the project will not be properly managed. All logic needs to be accurate. All durations must be correctly estimated. Additionally, best practices must be deployed when creating and updating a schedule. This requires strict attention to detail, brutal honesty, and a complete understanding of best practices, or the process falls apart.
Key Terms in CPM Scheduling
- Calendar: all activities are extended over a calendar across the top.
- Unique Identifier: each activity has a unique identifier (the number on the left). Without it, you could not assign the logic in the predecessor or successor columns.
- Activity w/ Description: CPM programs do not read words. The description is so you know what activity you are talking about. You must know what to call an activity in some structure to understand how to prioritize the activity.
- Relationship/Logic: explains the order in which activities can begin and end.
- Duration: how many days an activity will take.
- Non-Critical Activity: activities with room for delay (shown in blue)
- Critical Activity: activities with no room for delay (shown in red).
Essentially, building a schedule is, at a minimum, a three-step process for the user:
- Adding activities with names.
- Giving activity iterations.
- Assigning activity logic.
It helps to treat it as an Excel file because your schedule is a database. CPM 1) takes input, 2) plans over a calendar, and 3) calculates float, criticality, and start and finish dates. Note that you should never put in your own start dates or finish dates because it will ruin your schedule.
Learning to Build with Control
It’s not always easy to manage the constant change in a construction project. Projects inevitably run into unforeseen delays, cost overruns, and staffing extensions almost without fail. This is why you must use CPM as a communications tool for the entire project. It’s well-known that everyone on-site needs to be fluid as everything constantly changes, but the schedule ties everyone together.
Share