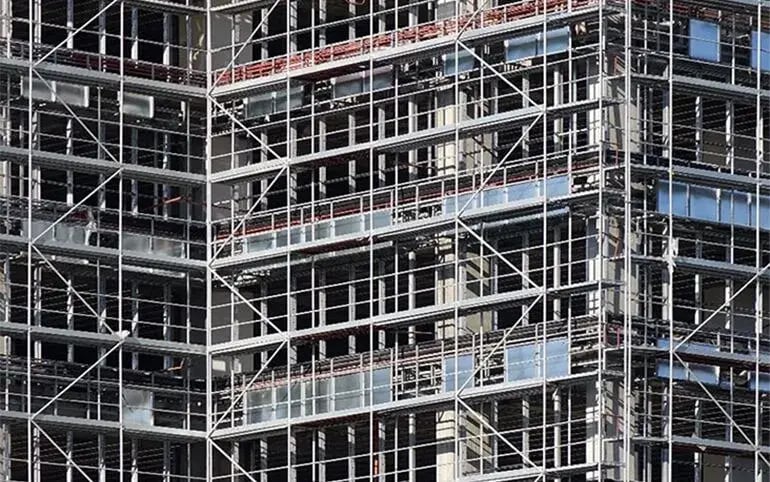
Blog
The Ultimate Guide to Reducing Construction Delays
Construction delays are inevitable, but the right mitigation strategies can help keep projects on track.

Delays in construction are more than just an annoyance – they’re costly and disruptive. They can lead to increased costs, strained relationships, and missed project deadlines. But the good news? Most delays can be avoided with proper planning, communication, and the use of advanced tools.
In this guide, we’ll break down the common causes of construction delays, their types, and actionable strategies to keep your projects on track.
What are Construction Project Delays?
A construction delay occurs when a project fails to meet planned milestones or completion dates, extending project activities beyond the planned schedule and affecting the overall timeline. These delays can result from various factors, including issues within the construction process, challenges faced by construction companies, and common causes like miscommunication or unforeseen events.
Different Types of Delays in Construction
Delays can vary significantly, and understanding their types helps with accountability and resolution. They can stem from various sources, such as adverse weather, labor shortages, or supply chain disruptions. Understanding the types of delays is key to managing accountability and resolving construction claims. Below are the primary categories of construction delays:
Excusable Delays and Non-Excusable Delays
Excusable Delays
Excusable delays are unforeseen events beyond the contractor’s control, which may justify a time extension without penalties. These delays often fall into the “force majeure” category and are sometimes compensable if caused by the project owner. Examples include:
- Labor strikes
- Natural disasters (e.g., hurricanes, earthquakes, floods)
- Changes initiated by the owner
- Errors and omissions in the plans, design documents, and specifications
- Differing site conditions or concealed conditions
- Lack of action by governmental or oversight bodies
- Intervention by outside agencies
For a detailed discussion on weather-related delays, refer to SmartPM’s article on weather delays in construction.
Non-Excusable Delays
Non-excusable delays result from factors within the contractor’s control. These delays may lead to penalties, additional costs, or breach of contract claims. Common examples include:
- Delayed mobilization
- Delayed submission of submittals
- Overall late performance and execution
- Late performance of subcontractors
- Late performance by suppliers
- Faulty workmanship by the contractor or subcontractor
Critical and Non-critical Delays
Construction schedule delays are classified based on their impact on the project timeline.
Critical Delays
Critical delays affect the project’s critical path and directly impact the completion date. These delays require immediate attention as they jeopardize project delivery and may result in claims. Examples include:
- Permit Approval Delays
- Weather Conditions
- Material Shortages
- Labor Strikes
Non-Critical Delays
Non-critical delays do not impact the critical path or overall completion date. However, they can still affect specific milestones, increase costs, or disrupt workflows if not managed properly. Examples include:
- Late Delivery of Non-Essential Supplies
- Minor Design Adjustments
- Equipment Malfunctions
- Administrative Backlogs
Compensable and Non-Compensable Delays
Compensable Delays
Delays caused by the project owner or their representatives, such as late approvals or design revisions, may entitle the contractor to compensation for time and costs incurred. Examples include:
- Changes to project scope or design initiated by the owner
- Late approvals or decisions from the owner affecting progress
- Failure to provide access to the construction site as agreed
- Delays due to errors or omissions in the provided design documents
- Suspension of work directed by the owner without justification
Non-Compensable Delays
Non-compensable delays are beyond both parties’ control, entitling only to a time extension. Examples include:
- Adverse weather conditions
- Natural disasters such as earthquakes or floods
- Utility service interruptions
- Acts of government or changes in regulations
- Labor strikes or shortages outside the contractor’s control
For more on handling delay disputes, see SmartPM’s guide on delay disputes .
Concurrent Delays
Concurrent delays occur when two or more delays overlap, complicating responsibility. For instance, if a contractor’s delay overlaps with an owner-caused delay, both parties may share responsibility.
Common Reasons For Construction Delays
There are seemingly infinite reasons for delays, but identifying the most common ones helps in prevention.
- Poor Planning: Inadequate scheduling and resource allocation.
- Project Complexity: Intricate designs or extensive scopes.
- Miscommunication: Lack of clarity among stakeholders.
- Labor Shortages: Insufficient or unavailable skilled workers.
- Supply Chain Issues: Delays in material procurement.
- Unrealistic Deadlines: Overambitious timelines leading to rushed work.
Best Practices to Avoid Construction Delays
Construction delays can be minimized through proactive planning, efficient resource management, and the use of advanced tools. By implementing these strategies, you can mitigate risks, prevent cost overruns, and achieve project milestones for a successful project. Below are key best practices to avoid construction delays:
Ensure Adequate Funding
Secure sufficient financing from the start to prevent work stoppages due to budget shortfalls. Adequate funding ensures that all phases of the project proceed smoothly and on time.
Manage Project Spending
Monitor expenses closely to avoid cost overruns. Regular budget reviews ensure financial resources are used effectively and help maintain progress within financial limits.
Utilize Construction Schedule Analytics Software
Employ tools like SmartPM to gain insights into project schedules, identify potential delays, and make data-driven decisions.
SmartPM’s analytics dashboard provides real-time insights into project timelines.
Manage a Realistic Project Scope
Clearly define project objectives and set achievable goals. A well-defined scope helps prevent scope creep, which can lead to delays and inflated costs.
Maintain Accurate and Reliable Data
Keep detailed records of project activities, decisions, and changes. Reliable data improves decision-making and informs better planning for future projects.
Manage Optimal Labor Allocation
Assign tasks based on workforce availability and expertise. Proper labor allocation ensures productivity and prevents bottlenecks during critical phases.
Practice Effective Communication and Planning
Maintain open lines of communication among all stakeholders, including contractors, subcontractors, and owners. Clear planning and alignment reduce misunderstandings and ensure timely problem-solving.
Stay on Top of Approvals and Project Bureaucracy
Proactively manage the approval process for permits, designs, and other documentation. Anticipating and addressing administrative requirements prevents unnecessary delays.
Account for Weather Factors and Seasons
Plan construction activities with weather conditions in mind. Understanding seasonal impacts allows for scheduling adjustments to avoid weather-related disruptions.
Choose Your Subcontractors Wisely
Select experienced and reliable subcontractors who can deliver quality work on schedule. Vetting subcontractors reduces the risk of rework and delays.
Recovering From Construction Delays
Recovering from construction delays is crucial to keeping projects on track, meeting the completion date, and maintaining stakeholder confidence. Effective recovery requires a proactive approach to minimize rework, adjust project timelines, and avoid future delays. This involves a mix of strategic project planning, clear communication, and focused resource allocation. Below are the key steps to navigate recovery:
Pinpoint the Root Cause
Identify the underlying issue causing the delay, whether it’s supply chain disruptions, workflow inefficiencies, or unforeseen site conditions. Understanding the root cause is critical to implementing a targeted solution.
Review Your Schedule and Budget
Assess the impact of the delay on the project timeline and budget. Identify critical path activities affected by the delay and evaluate how they influence the overall project completion date.
Create an Action Plan or Correction Plan
Develop a strategy to address the delay. This plan should include revised schedules, mitigation measures, and contingency steps to prevent similar setbacks in the future.
Allocate Resources Accordingly
Deploy additional resources, such as manpower, equipment, or materials, to critical activities that can expedite recovery. Prioritize tasks that have the greatest impact on regaining lost time.
Avoid Critical Mistakes and Construction Schedule Delays with SmartPM
SmartPM offers construction companies a comprehensive schedule delay analytics platform with a Windows-style day-for-day delay analysis engine built-in. Projects around the globe use SmartPM to monitor project progress, identify potential delays, and implement corrective actions that work, effectively maintaining control over project timelines and budgets. Ready to enhance your project management? Contact SmartPM today.
Frequently Asked Questions
-
Delays in the construction industry are highly common and occur across projects of all sizes and types. They are often caused by disruptions in workflows, supply chain issues, design changes, resource shortages, or inadequate project management. These delays can ripple through the entire project, negatively affecting performance, increasing costs, and extending timelines. The impact extends beyond the schedule itself—stakeholder relations can sour due to unmet expectations, and financial penalties or claims may arise from breaches of contracts. On an industry-wide scale, delays highlight inefficiencies and the need for more resilient planning, improved communication, and better risk management strategies.
-
Lag in a construction schedule refers to a planned delay or gap between two dependent activities. It can be positive (a delay) or negative (an overlap), influencing the timing of the successor activity. While lag serves practical functions, such as accommodating curing times for concrete or delivery delays for materials, excessive or poorly planned lag may signal inefficiencies or poor schedule development. Effective use of lag helps maintain the project’s functionality and aligns tasks for seamless execution, ultimately safeguarding the project’s completion date. However, project planners should carefully monitor and document lag to ensure it doesn’t mask scheduling errors or lead to unrealistic timelines.
Share